1994ch
Well-Known Member
Got it fixed!!! was a scratch on the seat of the line. Was able to burnish it out and it sealed. Used a piece of sandpaper and an old injector, placed the paper over the seat in the injector and pushed the line into it while twisting. Would have used valve lapping compound, but could not find it. Cleaned the line out really well (did not figure the injector would like sandpaper for lunch) and let it run for a while with no drips.
Could not find a 6.2 air filter housing so I am modifying a gasser housing to fit. Got an adapter plate welded up, then will cut out the center of the old filter housing and weld the adapter plate in. The center hole on the housing is about 1/2 in larger for the 6.2. I will trim the adapter flange into a circle of course.... its dark outside and my camera does not like the low light but it should give you the idea of what it will look like.
I plan to get a turbo on this eventually, but I have gone way over budget so I am going to wait on the turbo and exhaust system and just make do with what I have for now. The tahoe originally had a dual exhaust so I think it should not be too restrictive (have to modify it a bit as well.... cut out the cats, etc)
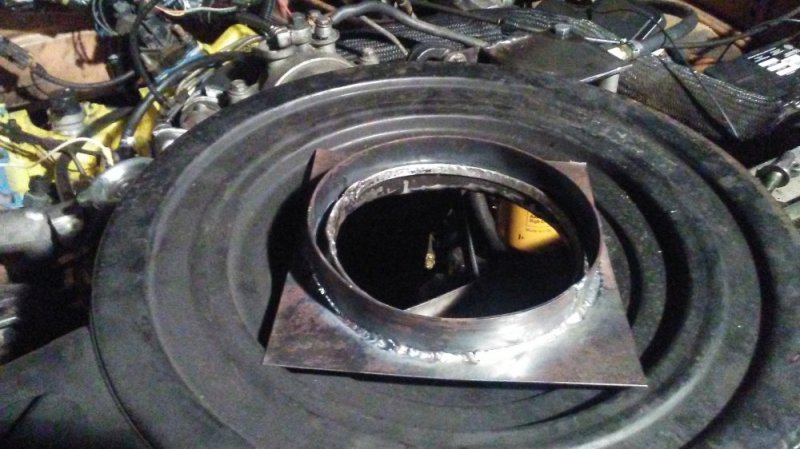
Could not find a 6.2 air filter housing so I am modifying a gasser housing to fit. Got an adapter plate welded up, then will cut out the center of the old filter housing and weld the adapter plate in. The center hole on the housing is about 1/2 in larger for the 6.2. I will trim the adapter flange into a circle of course.... its dark outside and my camera does not like the low light but it should give you the idea of what it will look like.
I plan to get a turbo on this eventually, but I have gone way over budget so I am going to wait on the turbo and exhaust system and just make do with what I have for now. The tahoe originally had a dual exhaust so I think it should not be too restrictive (have to modify it a bit as well.... cut out the cats, etc)
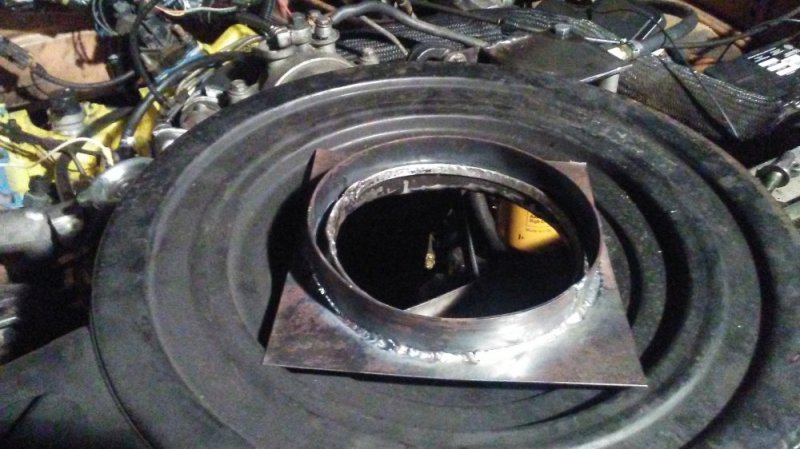