n8in8or
I never met a project I didn’t like
Then I plugged the Cleco holes.
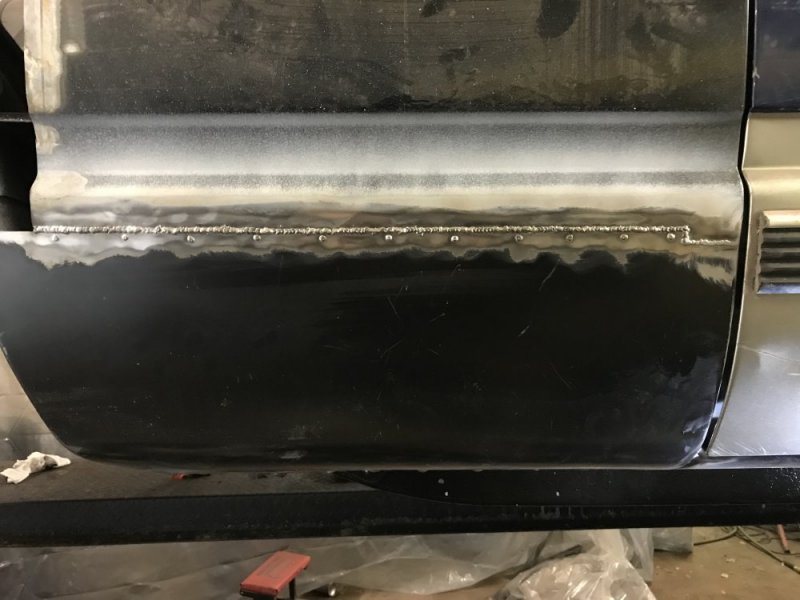
Next was grinding. I ground just a little at a time with an 80 grit 4.5” flap wheel so as not to put too much heat into the panel. I followed that up with a 3” angle grinder and roloc discs for fine touch-up.
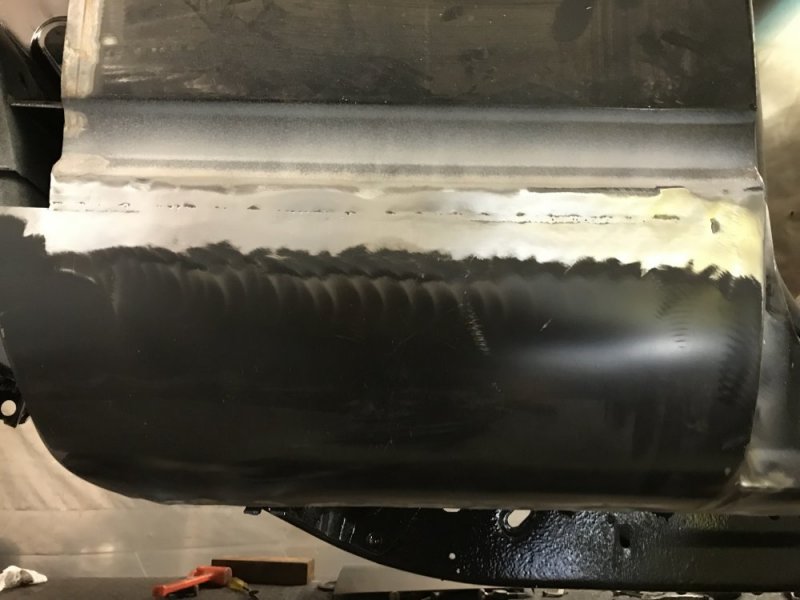
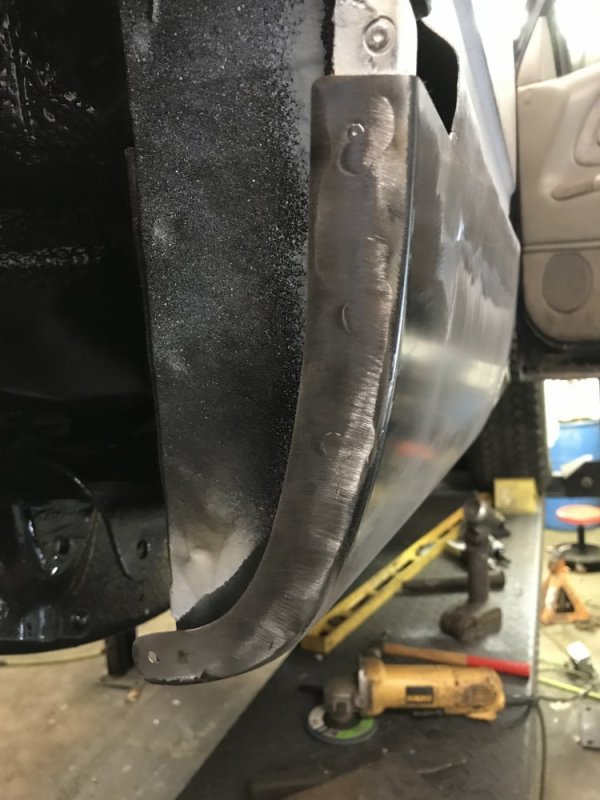
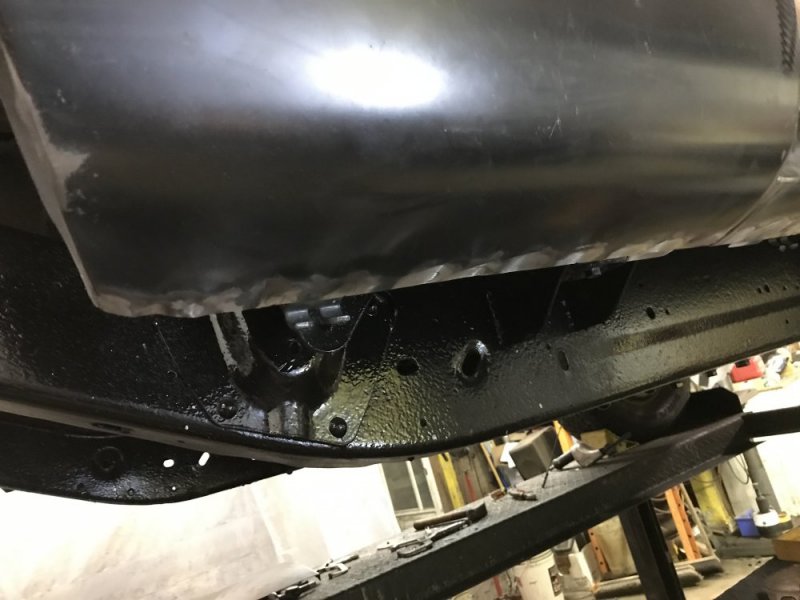
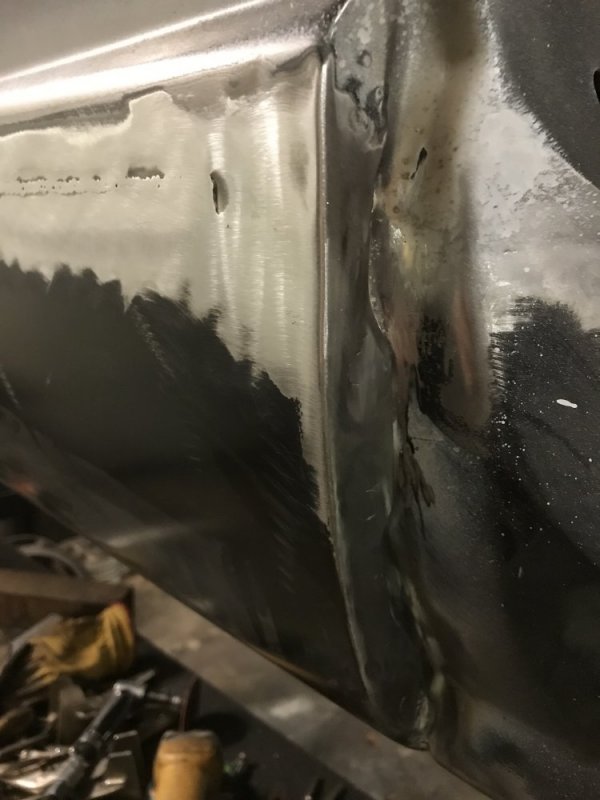
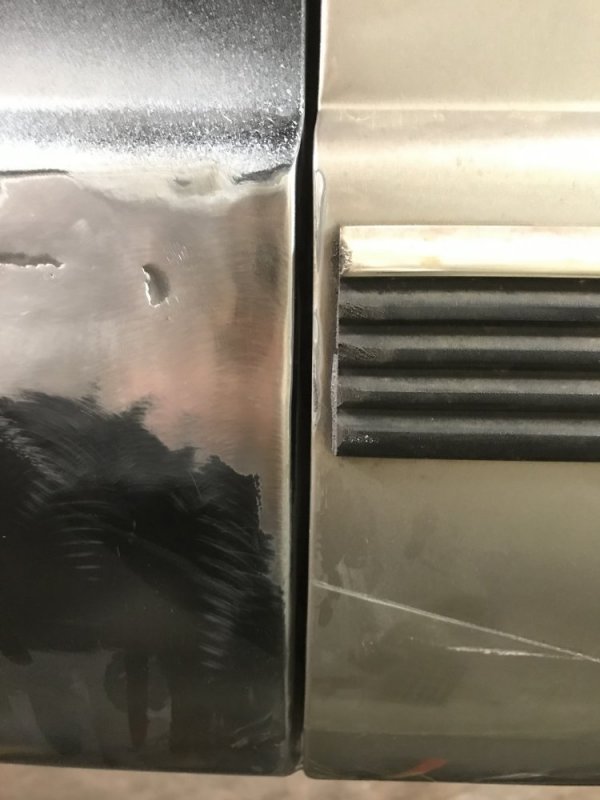
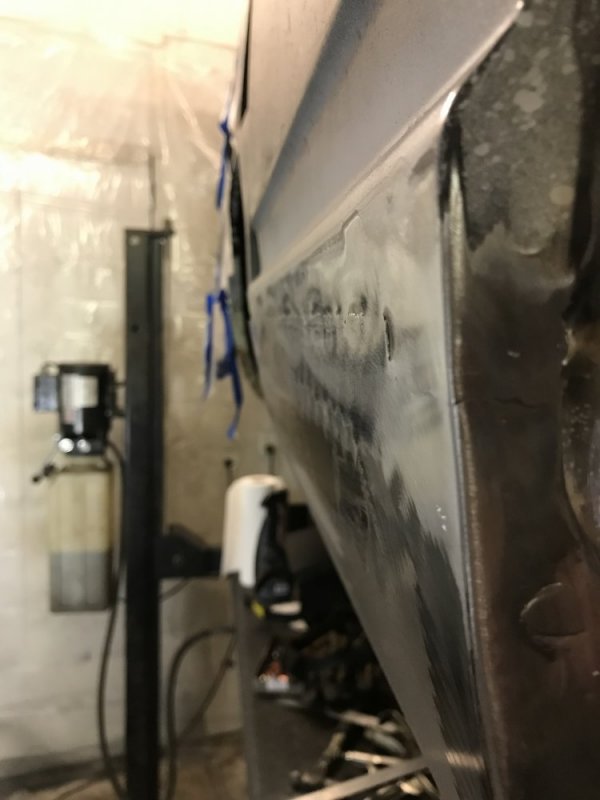
Even though I really tried to be careful with heat, the panel still warped. Now I didn’t check how straight it was before welding so it’s possible it was warped already, but I can’t say that for sure. I will check this before welding on the other side and be more careful with heat.
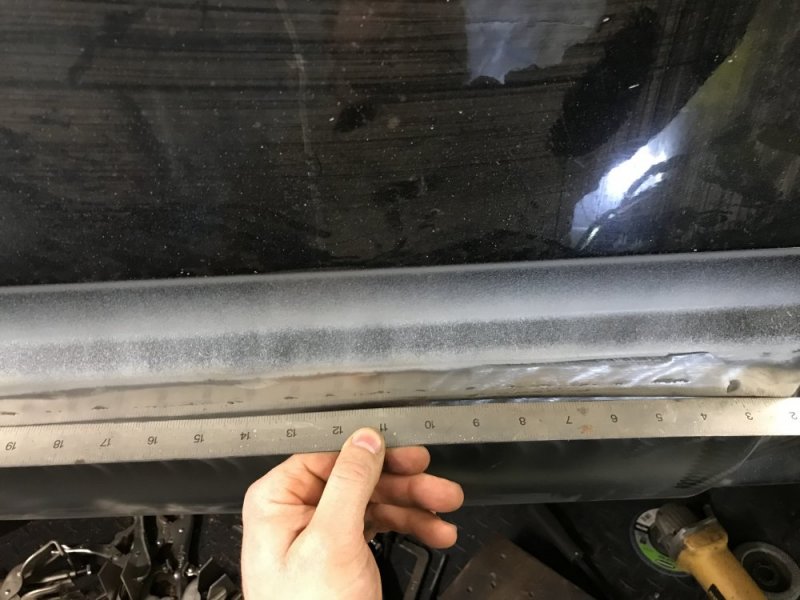
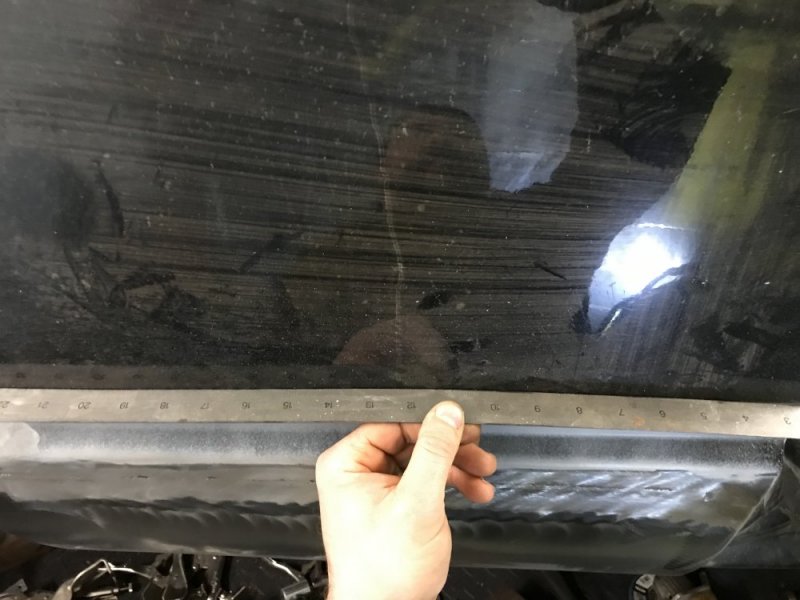
I really did expect to get it better than this, but it’s still not terrible. I will try pulling the low spots out so I don’t have to use much filler to dial it in when it comes time for body work.
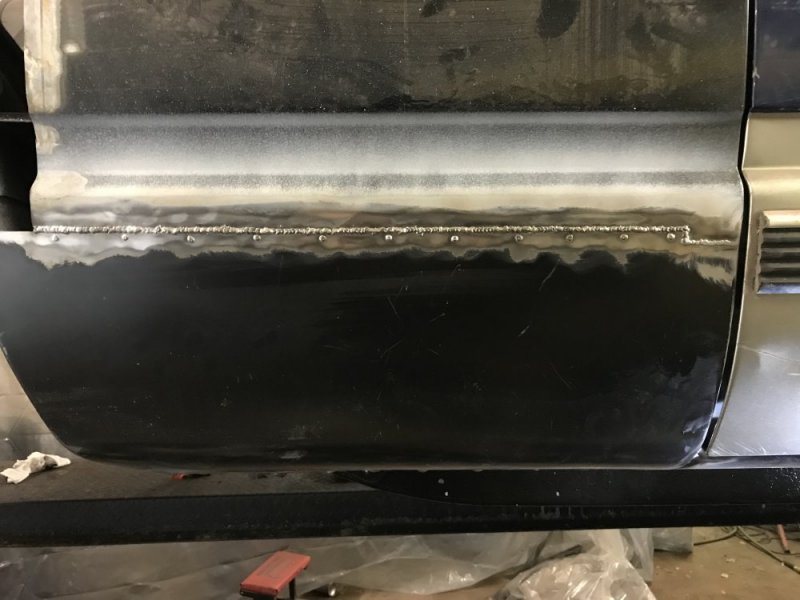
Next was grinding. I ground just a little at a time with an 80 grit 4.5” flap wheel so as not to put too much heat into the panel. I followed that up with a 3” angle grinder and roloc discs for fine touch-up.
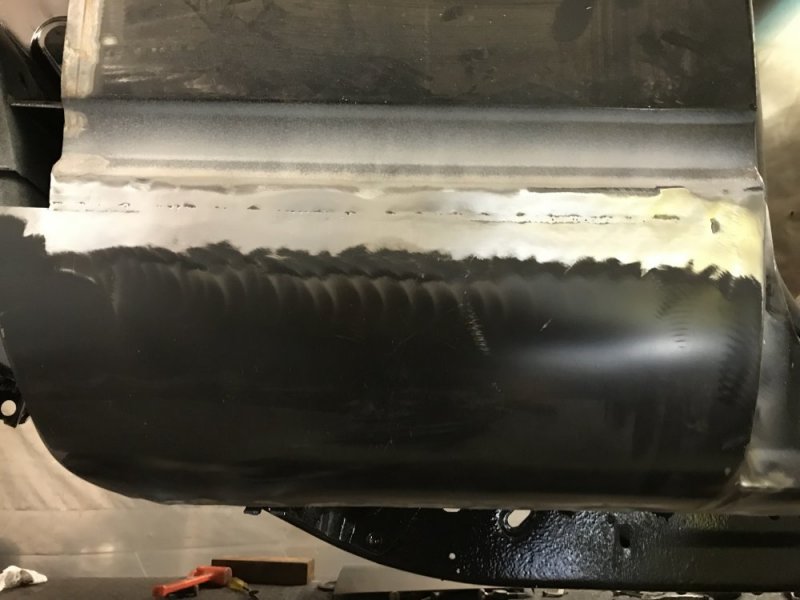
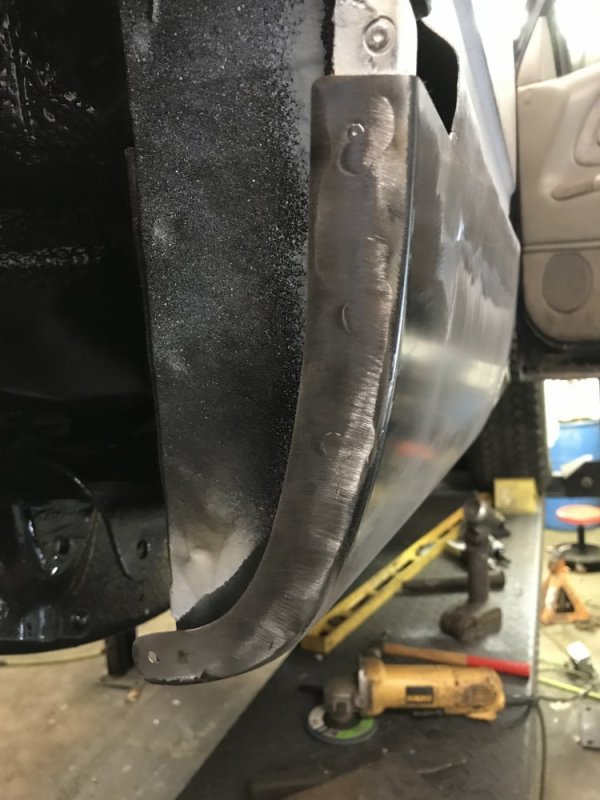
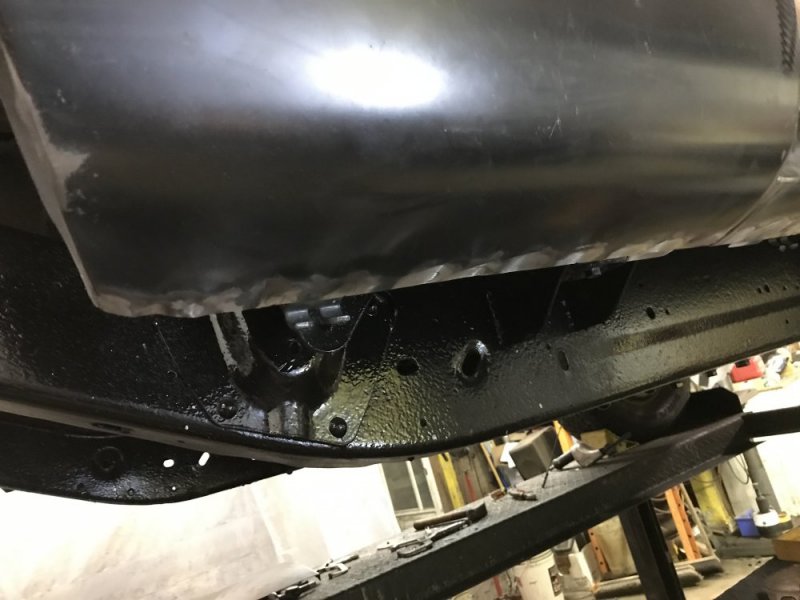
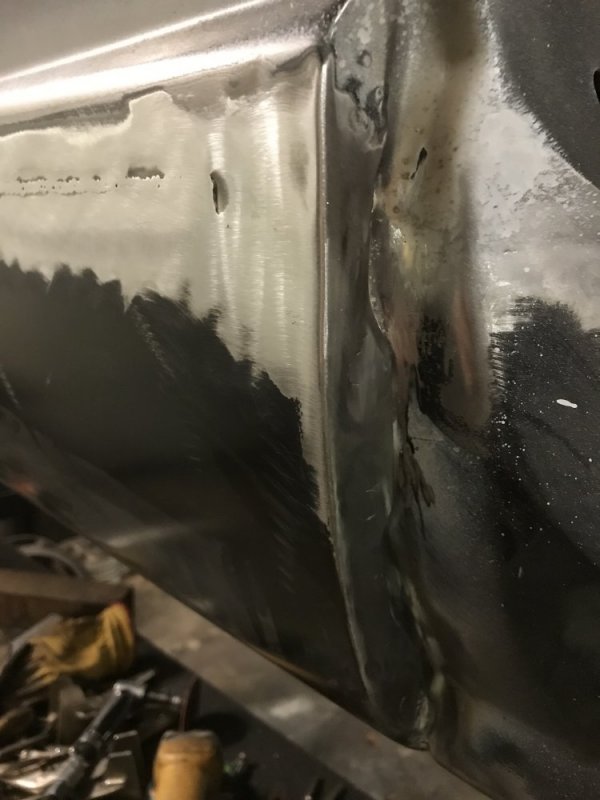
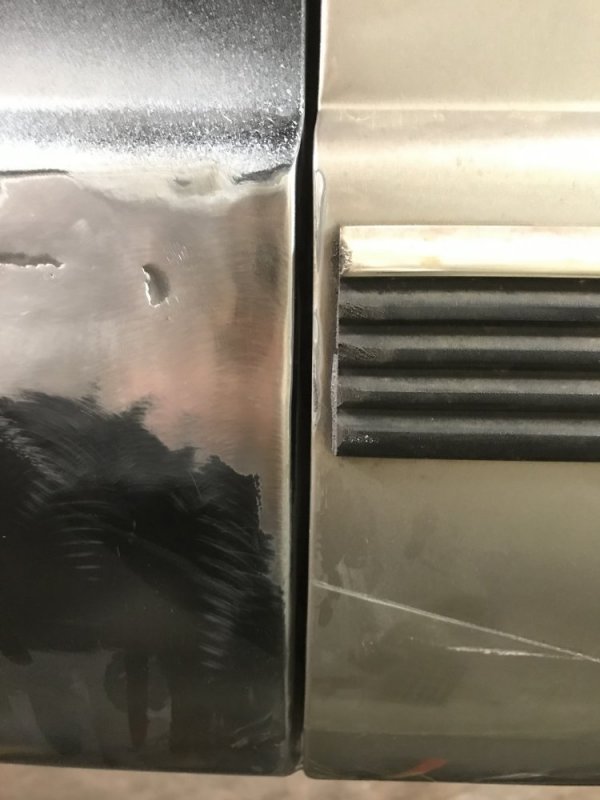
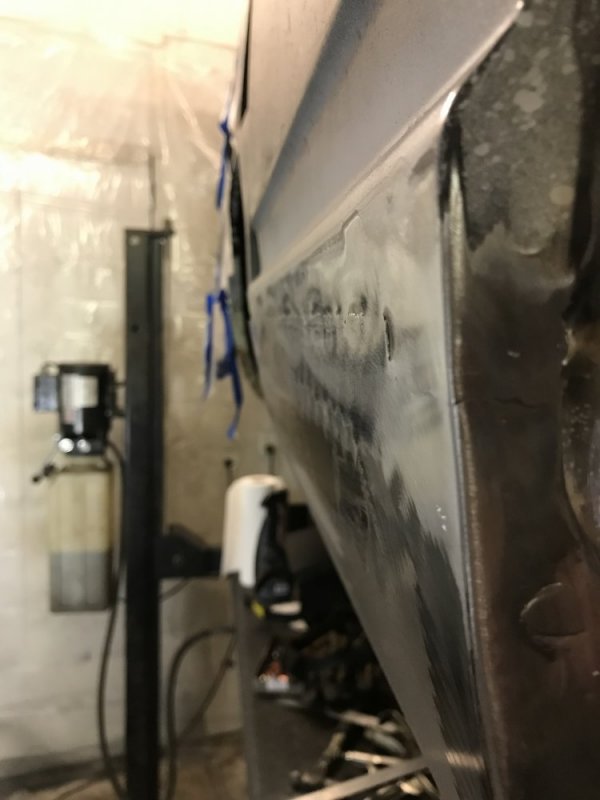
Even though I really tried to be careful with heat, the panel still warped. Now I didn’t check how straight it was before welding so it’s possible it was warped already, but I can’t say that for sure. I will check this before welding on the other side and be more careful with heat.
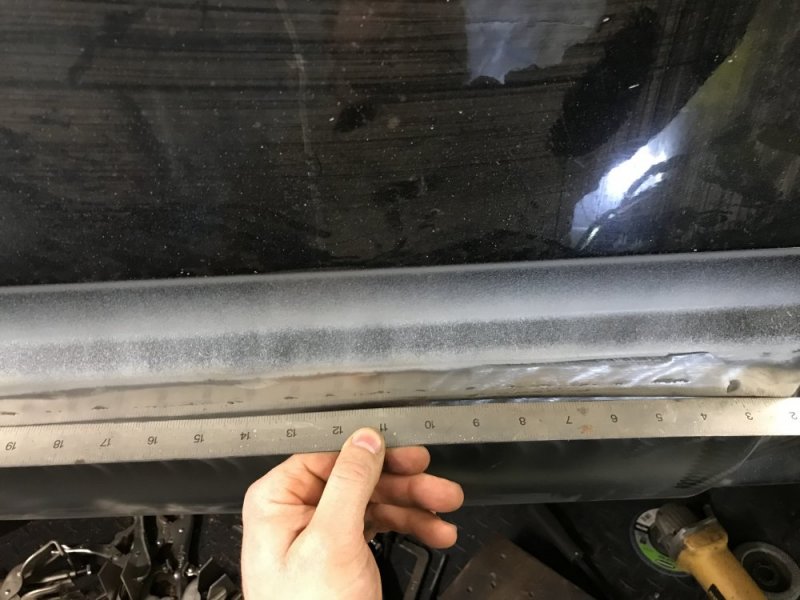
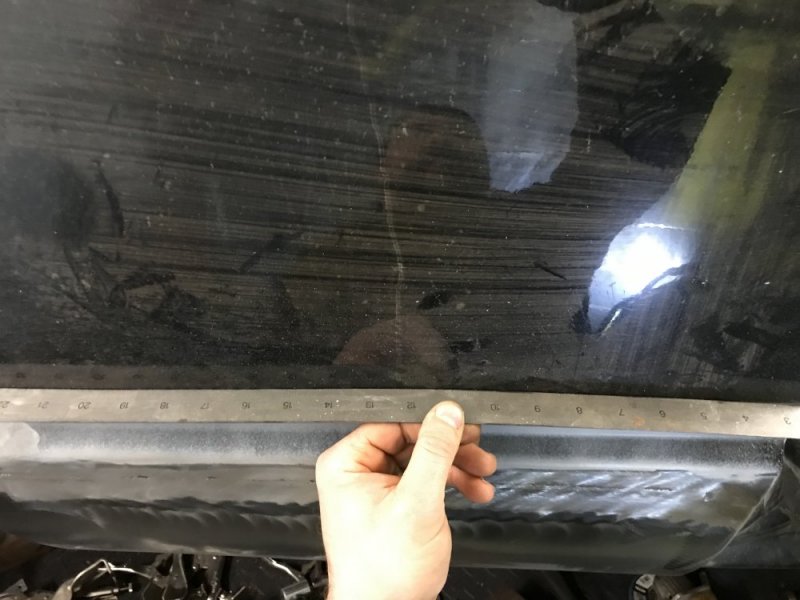
I really did expect to get it better than this, but it’s still not terrible. I will try pulling the low spots out so I don’t have to use much filler to dial it in when it comes time for body work.