n8in8or
I never met a project I didn’t like
I got the panel seam ground down today. I started with the 4-1/2” flap wheel as before, but then used a 3” flap wheel on an angle die grinder to finish it. When I was scrounging in my abrasives drawer I found those 3” discs which I had totally forgotten about purchasing months ago! They worked a ton better for finishing than the Roloc discs. Of course the HF die grinder died just a couple minutes in so I had to run out and get another one so that used up some of my project time today.
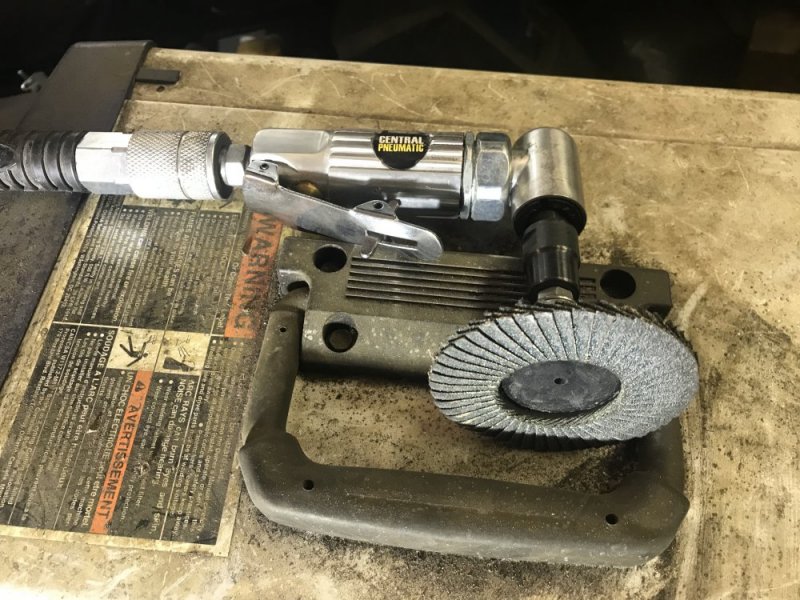
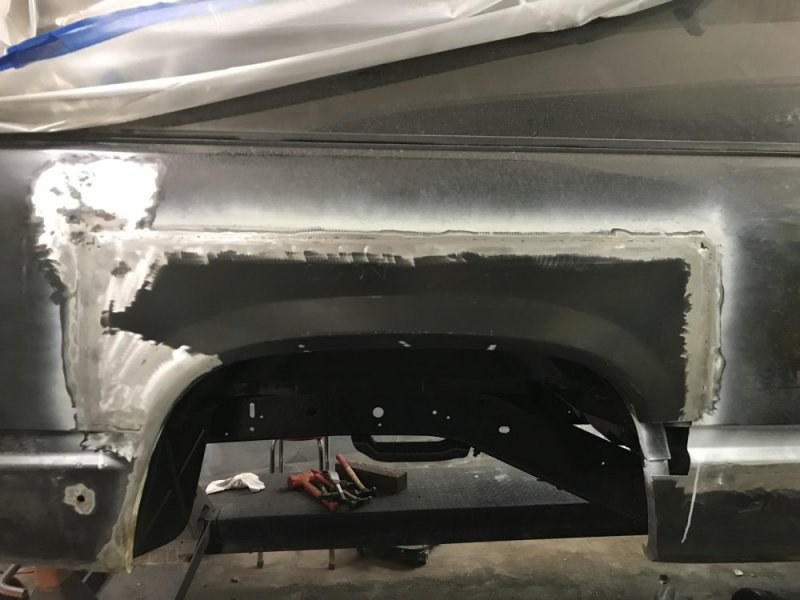
Last thing I did was add the flange to the driver side panel. The flanger is definitely warping the panel so that sucks, but I still think it’s the best way for me to tackle the job.
Here’s a before pic of the panel:

And here’s after:
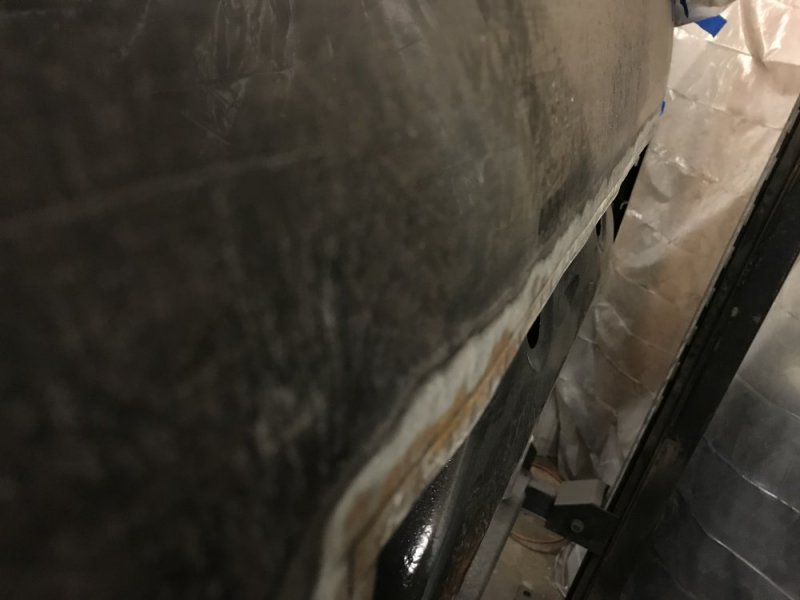
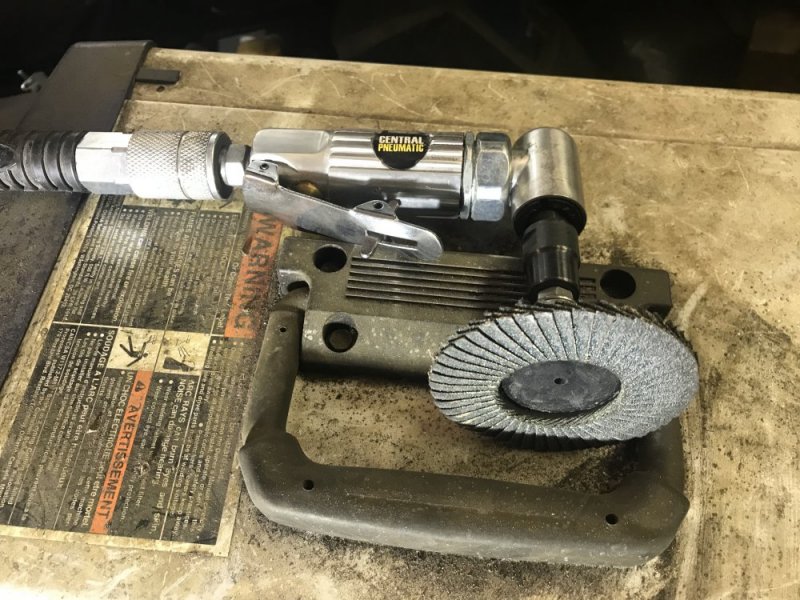
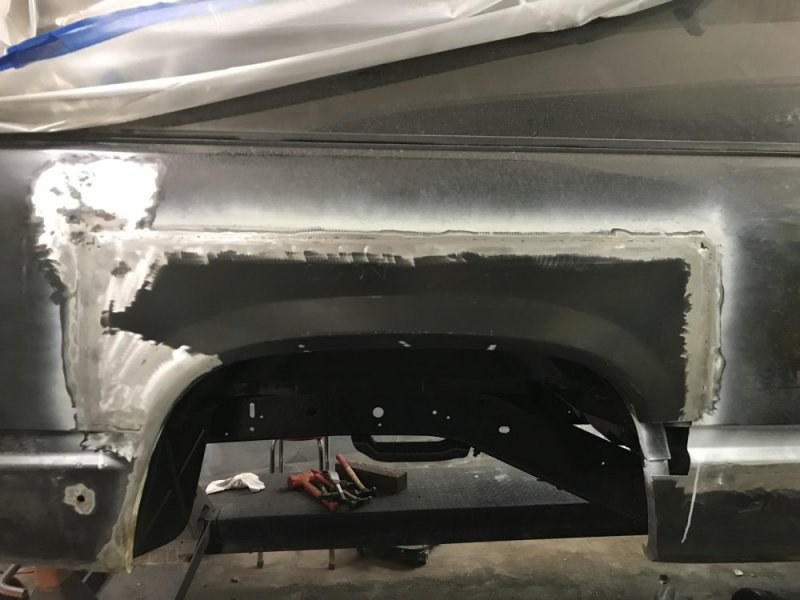
Last thing I did was add the flange to the driver side panel. The flanger is definitely warping the panel so that sucks, but I still think it’s the best way for me to tackle the job.
Here’s a before pic of the panel:

And here’s after:
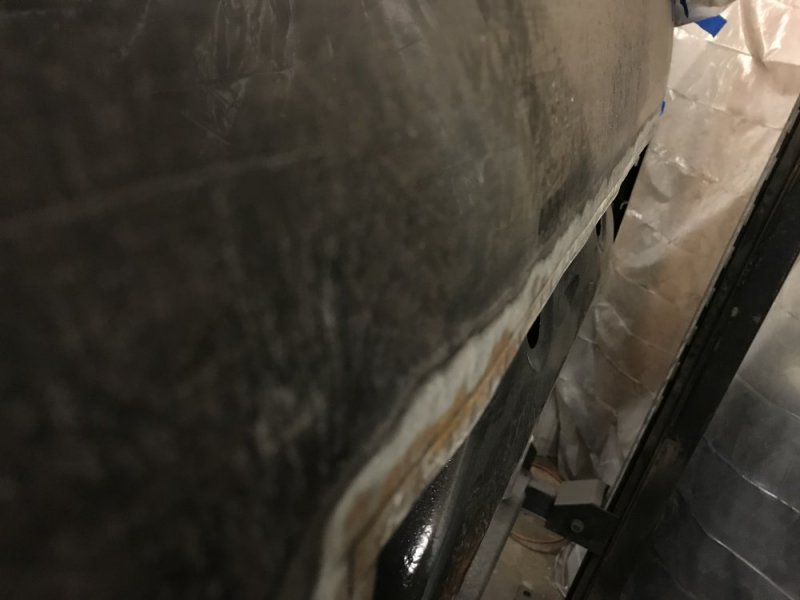