MrMarty51
Well-Known Member
It was a very slight amount that I removed from the pump.on the pics you posted I could not tell where you ground out on the pump to match the ports of the backing plate. can you post were you ground into?
on that one that you said wasn't cooling well it kinda looks like the impeller is slightly out on the shaft where the others look like the shaft is protruding out slightly further than the impeller. if there is a larger gap under the impeller to the pump body, that might explain why it's not pushing as much coolant flow as the others. I would think it's not just the gap on the sides of the impeller but also the gap behind it to the body too.
My thinking is the only real way to test flow and balance would be to have someone mock up a pump and timing cover not attached to an engine but have it in such a way flow meters could be attached to each outlet of the pump where it meets the block and use a motor to drive the pump monitoring flow on each side. taking into account that some flow from the pump on the hose bib for the heater would come from one side or the other. I bet we have members here who could do such a thing, it would be interesting to see results of that.
This is the before picture.
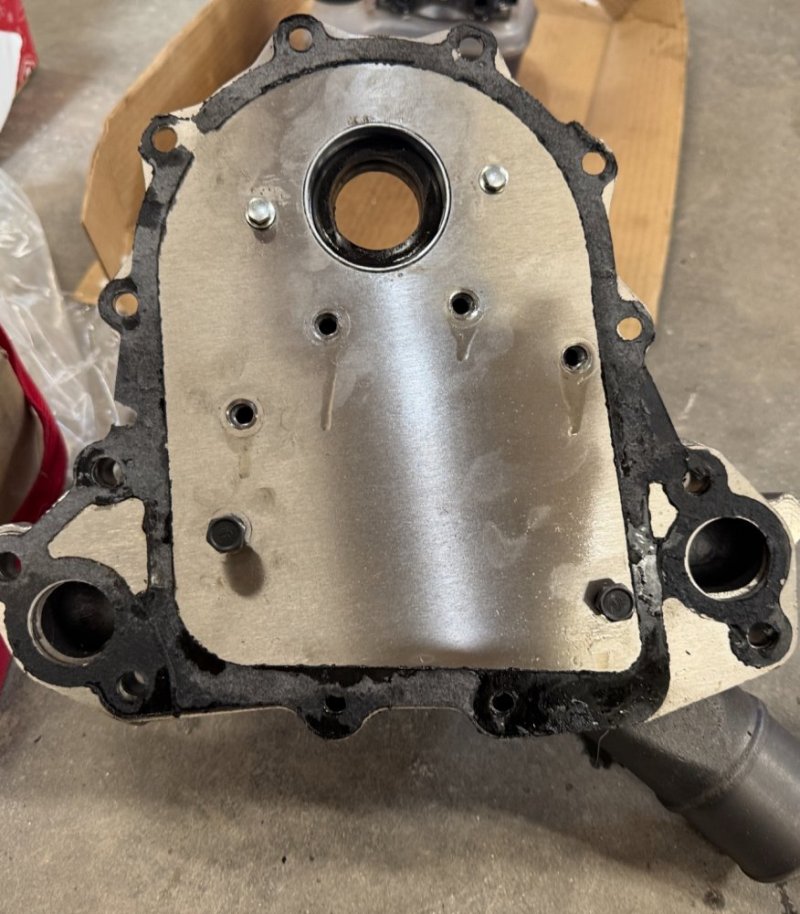
And the after.
The new Delco pump was a real close match and most likely would have caused no problems.
But this should give a smooth transition.
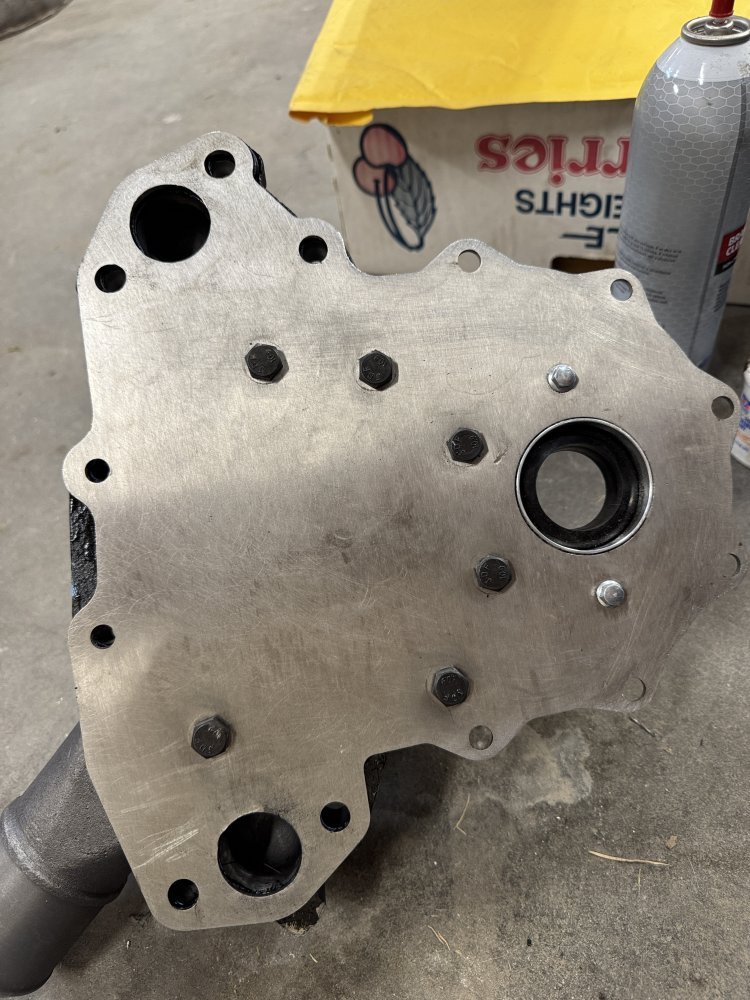
How about sealent on the bolt threads.
Guess I could install them dry then if there is any seepage use a very slight amount of aluma seal.
I did use some of the nickel anti seize when I put it together.