n8in8or
I never met a project I didn’t like
Slow progress this past week, but I’m sitting pretty good right now.
Rather than dive right into the short block I instead decided to start getting the truck ready to receive the drivetrain. So I reran harnesses and installed new power steering hoses and cooler. I also reinstalled all of the crossmembers I had removed for the frame derusting.
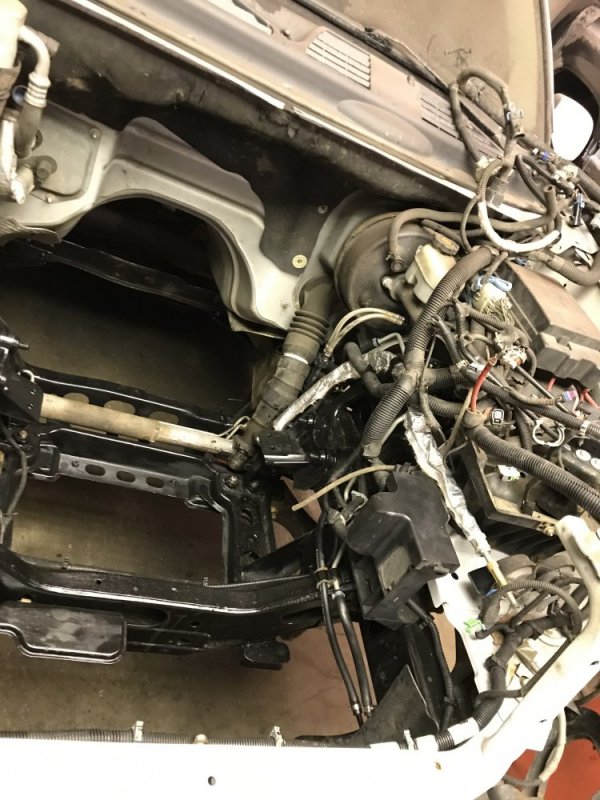
I also have all new seals installed in the front diff and front intermediate shaft bearing.
Then today I finally finished up the short block. I checked the ring gaps and connecting rod bearing clearances and got all the pistons and rods installed and torqued down. The rods are the later model floating rods that are stronger. I bought a set that had been refurbished by a place that sells them on eBay. Then I had the machine shop fit ARP rod bolts and hone them round again. These rods are a cracked cap design so they can’t resize the big end like a typical rod - they hone them .002” oversize and there is a special oversized bearing available to fit. My clearances were .002” on all of my jounals so everything was all good there. I went with the dished pistons so I can have a reasonable compression ratio to run 87 octane now and then later on I can swap heads and regap the rings and it’s ready for some turbo fun. The whole rotating assembly is balanced.
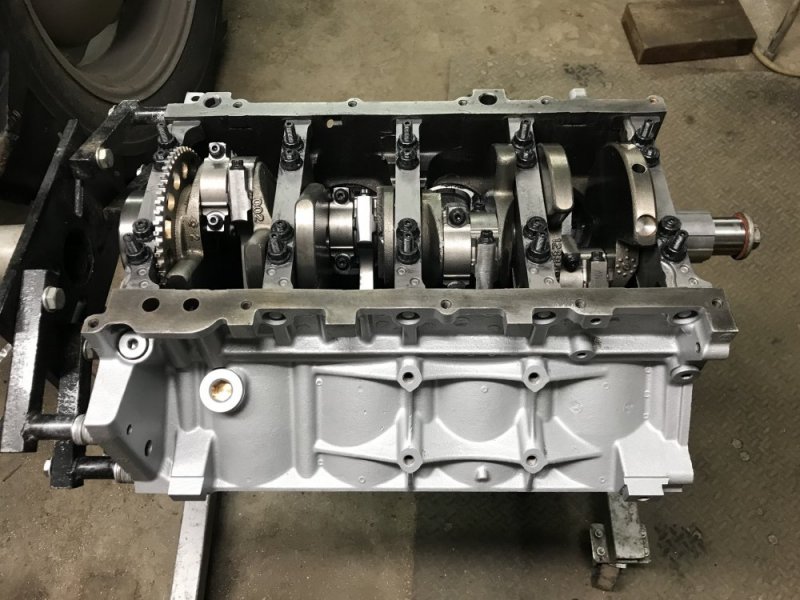
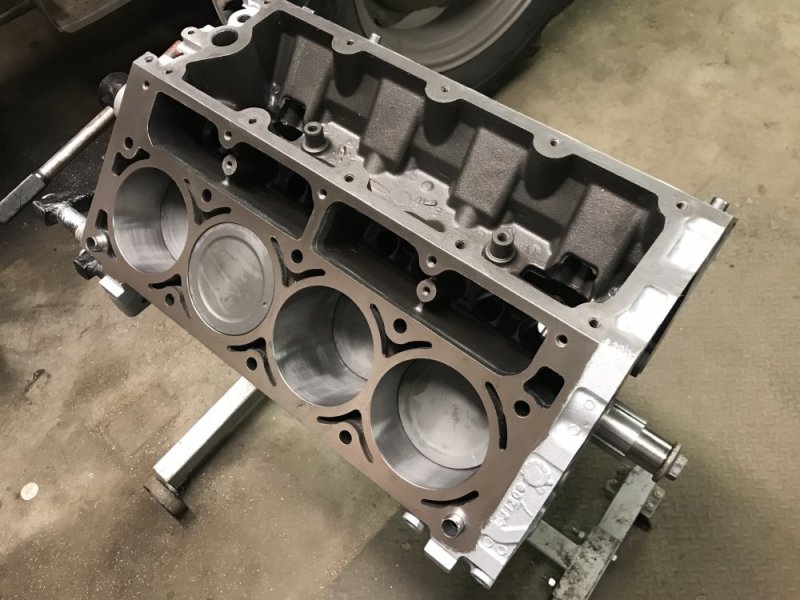
Next I started on the oil pan. This chassis has a front sump oil pan. Trailblazer SS’s have a problem with oil starvation on launch because the oil sloshes away from the oil pump pickup. For AWD/4WD, you can either buy a $300 extended pickup or a $25 baffle. I went with the baffle. So today I installed the baffle and replaced the gaskets for the oil filter adapter in the pan.
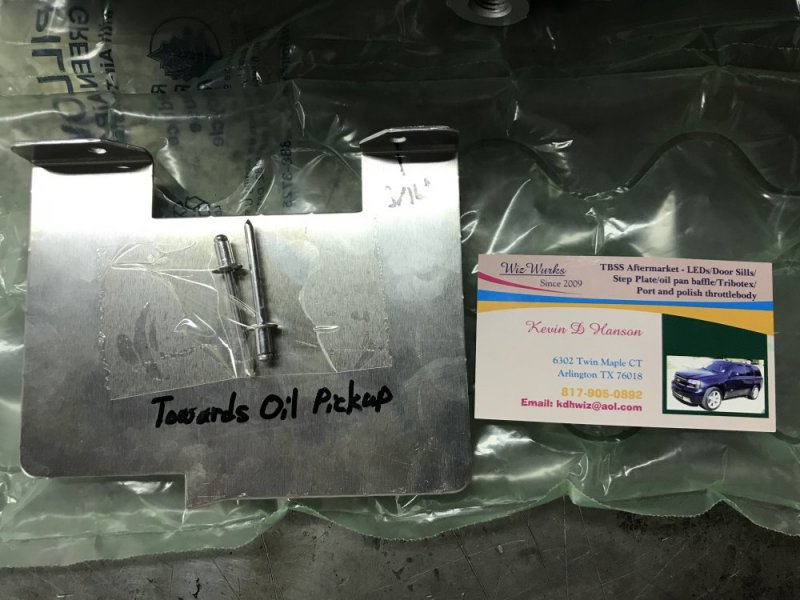
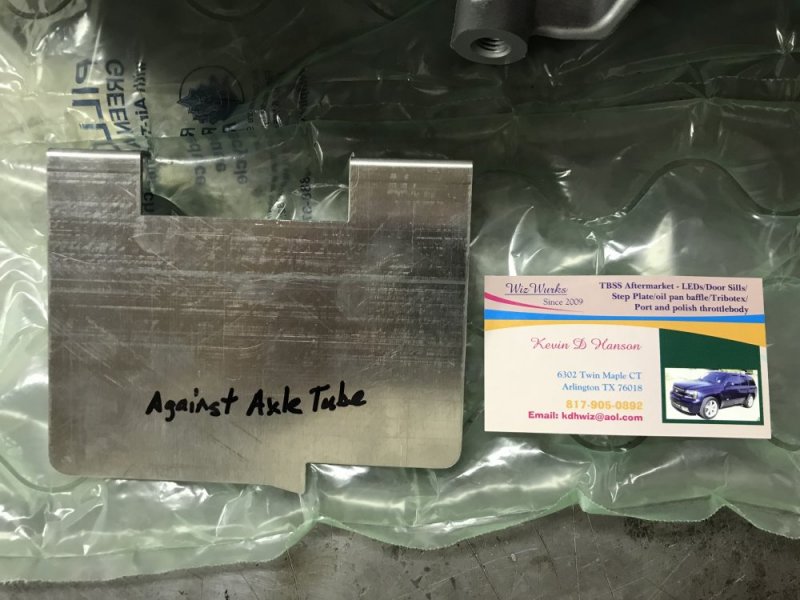
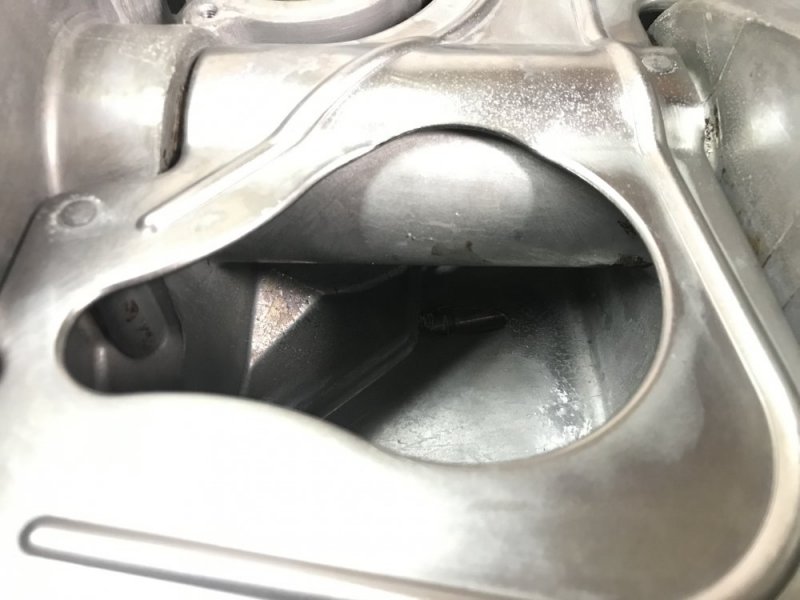
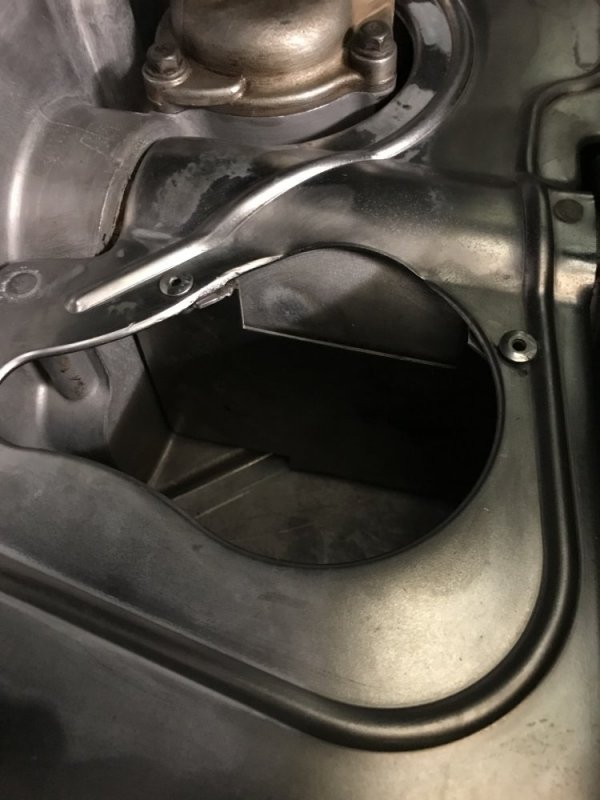
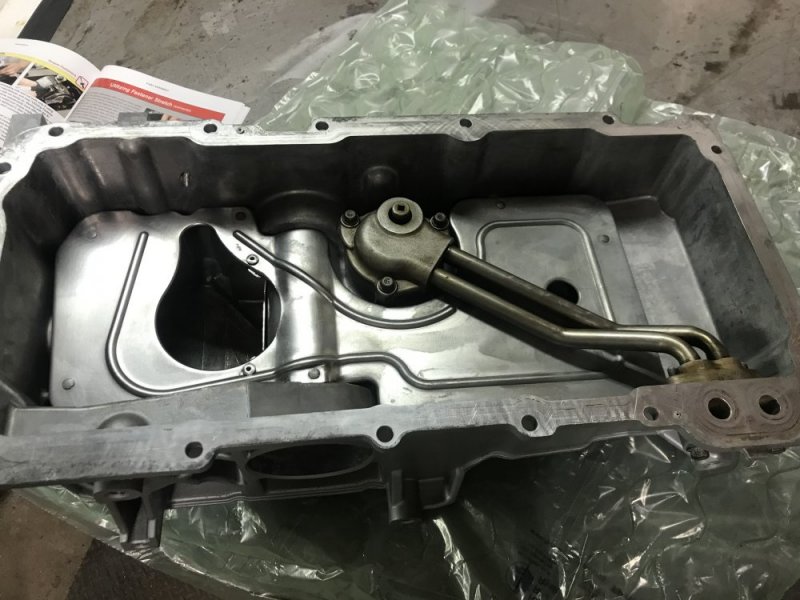
The final thing I did was start replacing U-joints. The front shaft is done and the joints are removed from the rear shaft - I’ll install them tomorrow.
My cam is supposed to be coming in this week and the machine shop was also hoping to have my heads done by the end of the week. If both of those things actually happen and my piston-to-valve clearance is OK, I should have the engine assembled and the engine/trans installed next weekend. Then a couple more days of buttoning up and then it will be ready for tuning! I can finally see the light at the end of the tunnel.
Rather than dive right into the short block I instead decided to start getting the truck ready to receive the drivetrain. So I reran harnesses and installed new power steering hoses and cooler. I also reinstalled all of the crossmembers I had removed for the frame derusting.
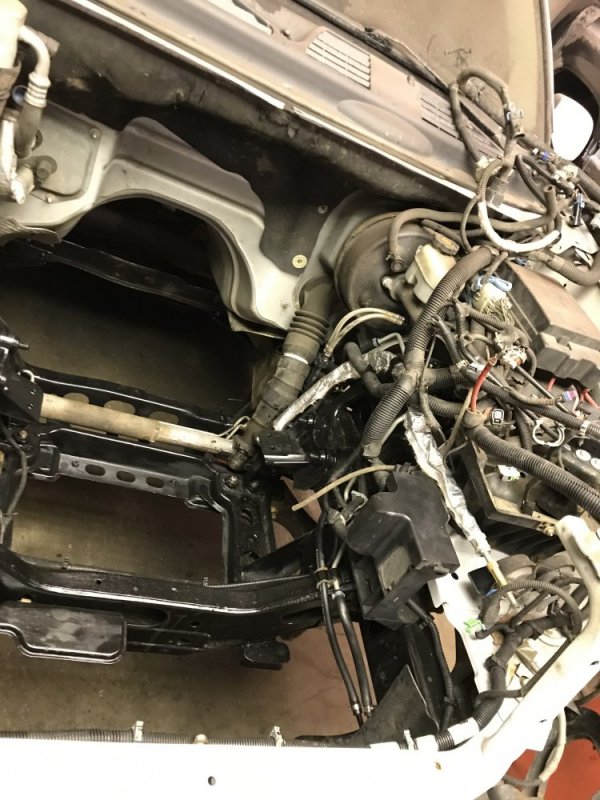
I also have all new seals installed in the front diff and front intermediate shaft bearing.
Then today I finally finished up the short block. I checked the ring gaps and connecting rod bearing clearances and got all the pistons and rods installed and torqued down. The rods are the later model floating rods that are stronger. I bought a set that had been refurbished by a place that sells them on eBay. Then I had the machine shop fit ARP rod bolts and hone them round again. These rods are a cracked cap design so they can’t resize the big end like a typical rod - they hone them .002” oversize and there is a special oversized bearing available to fit. My clearances were .002” on all of my jounals so everything was all good there. I went with the dished pistons so I can have a reasonable compression ratio to run 87 octane now and then later on I can swap heads and regap the rings and it’s ready for some turbo fun. The whole rotating assembly is balanced.
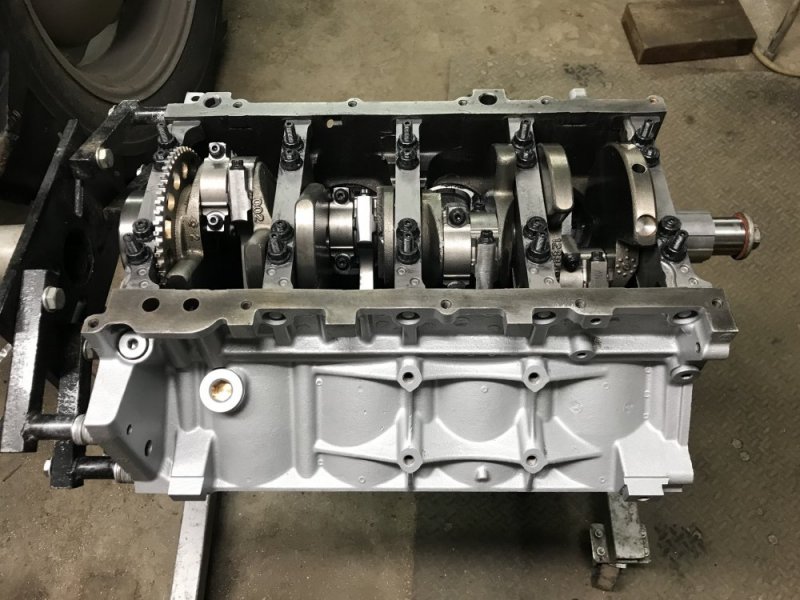
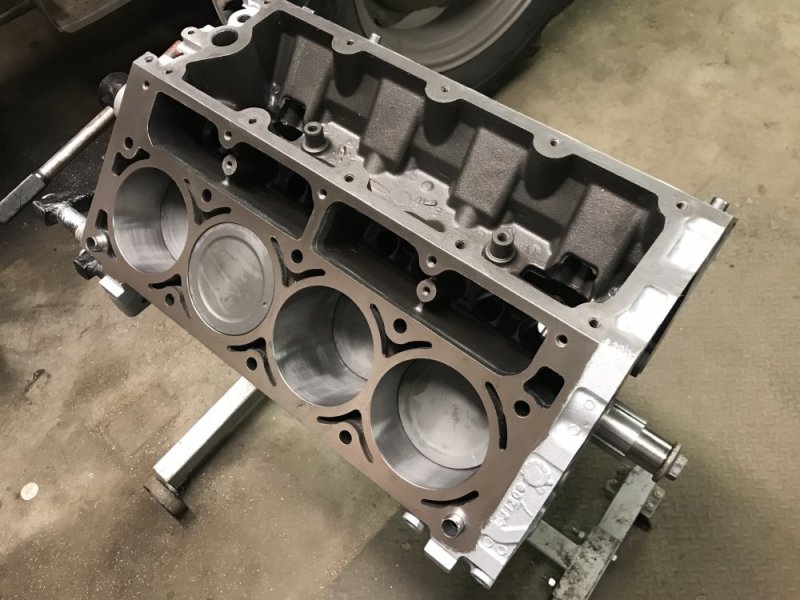
Next I started on the oil pan. This chassis has a front sump oil pan. Trailblazer SS’s have a problem with oil starvation on launch because the oil sloshes away from the oil pump pickup. For AWD/4WD, you can either buy a $300 extended pickup or a $25 baffle. I went with the baffle. So today I installed the baffle and replaced the gaskets for the oil filter adapter in the pan.
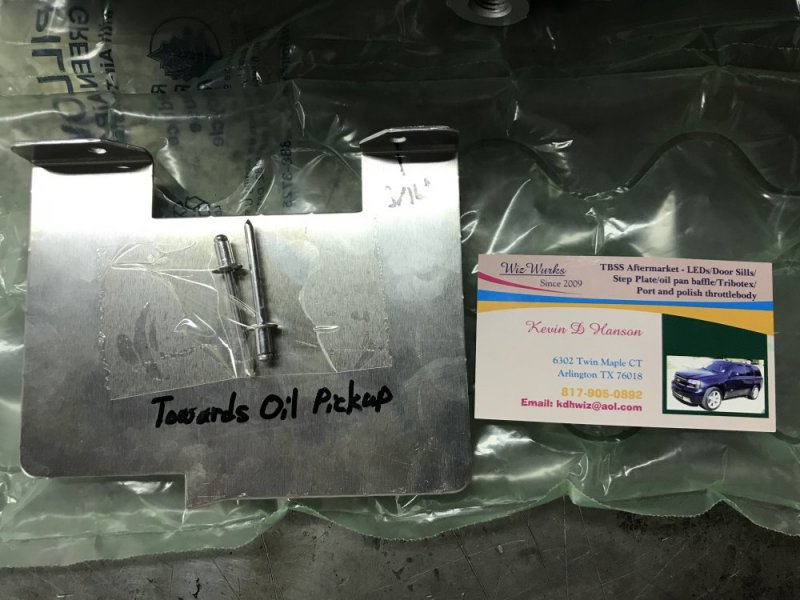
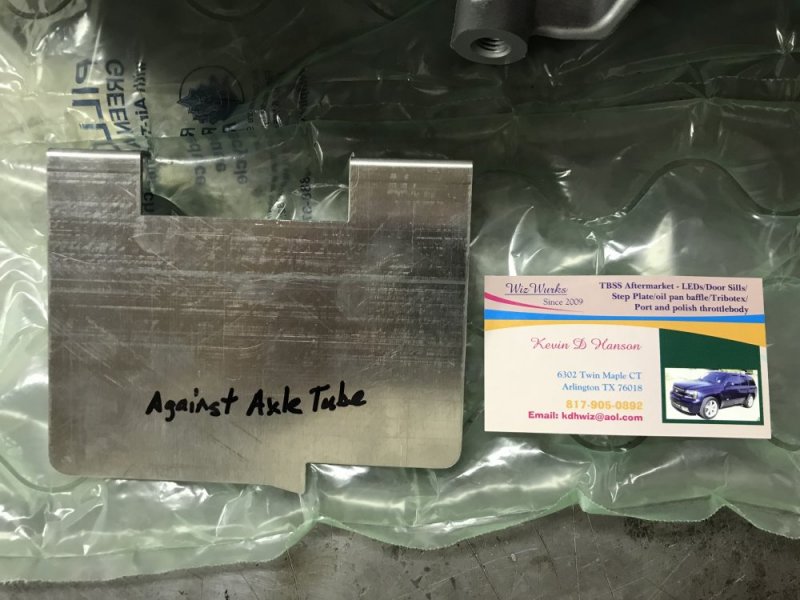
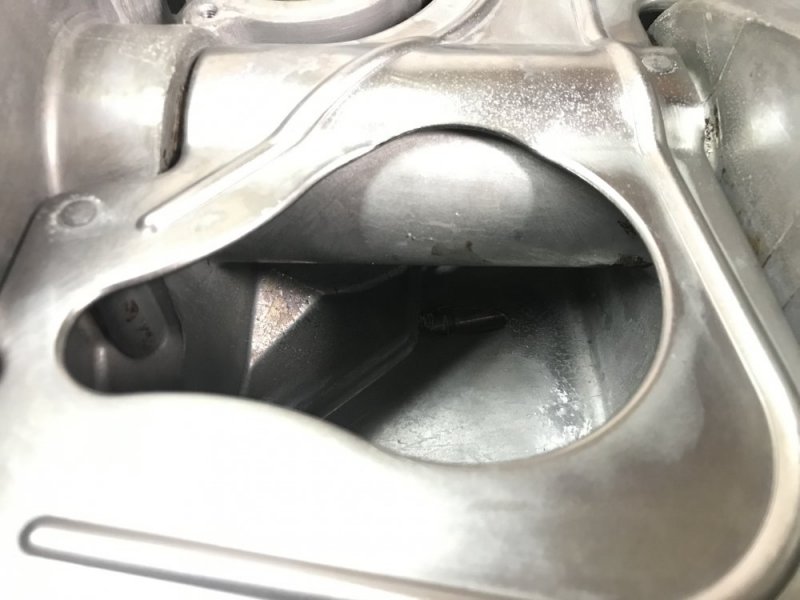
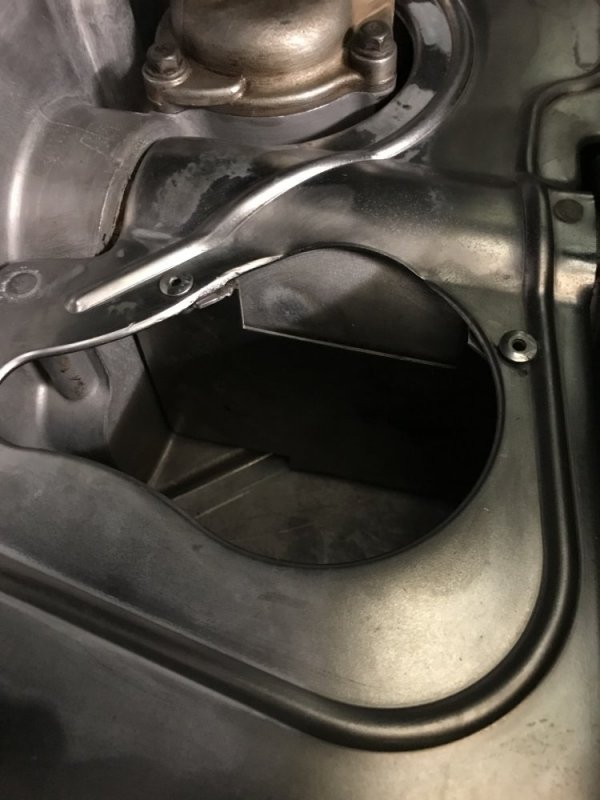
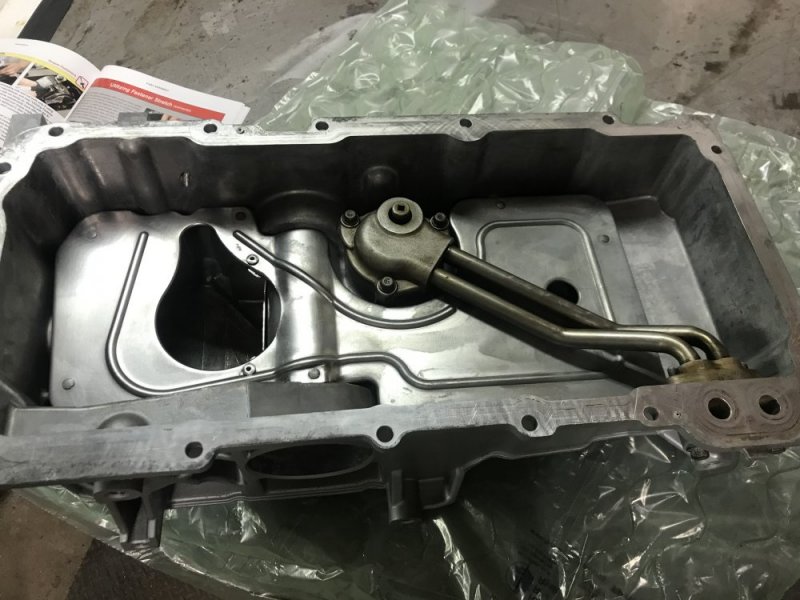
The final thing I did was start replacing U-joints. The front shaft is done and the joints are removed from the rear shaft - I’ll install them tomorrow.
My cam is supposed to be coming in this week and the machine shop was also hoping to have my heads done by the end of the week. If both of those things actually happen and my piston-to-valve clearance is OK, I should have the engine assembled and the engine/trans installed next weekend. Then a couple more days of buttoning up and then it will be ready for tuning! I can finally see the light at the end of the tunnel.
