Clearly built for the assembly line and no concern what-so-ever for repair. Videos give options of dropping the subframe or raising the engine via pass side engine mount disconnect and removing the alternator.
Seriously you need to make a video for a paragraph of text?!
All Google wants to feed one nowadays is 10,000 Youtube videos that are 5 min of suck before we get to the point.
Anyway got a 2007 Saturn Vue to replace the compressor on. Fighting it for a few years. First the AC Compressor Control Solenoid Valve failed in the "no cool at idle" position. You can get this part kit alone off fleabay or other places. You can change the valve by recovering the system, unbolting the compressor, and then the tilt of the compressor allows you to get to the valve located in the rear of the compressor from under the vehicle.
Couple years later the system lost it's charge with PAG oil all over the front of the compressor. A *cheep* recharge held another couple years.
Now it's time to rip the leaking compressor out. (The dryer is located behind the driver's side headlight. The headlight hooks the front bumper requiring some of the grille to be taken apart.) We removed the air cleaner box, timing belt cover, alternator, knocking the wire hold down on the rear of the alt off, then popping the two engine mount nuts off, top alternator bracket to valve cover, separating the AC line mid engine, removed tensioner pulley, and raising the engine some.
We used a section of scrap extension cord for a rope threaded through the compressor bolt holes to help pull the SOB out. The ports need to be rotated to the sky and clutch comes out first around the alt bracket. The AC hose needs to be moved out of the way taking 3 hands.
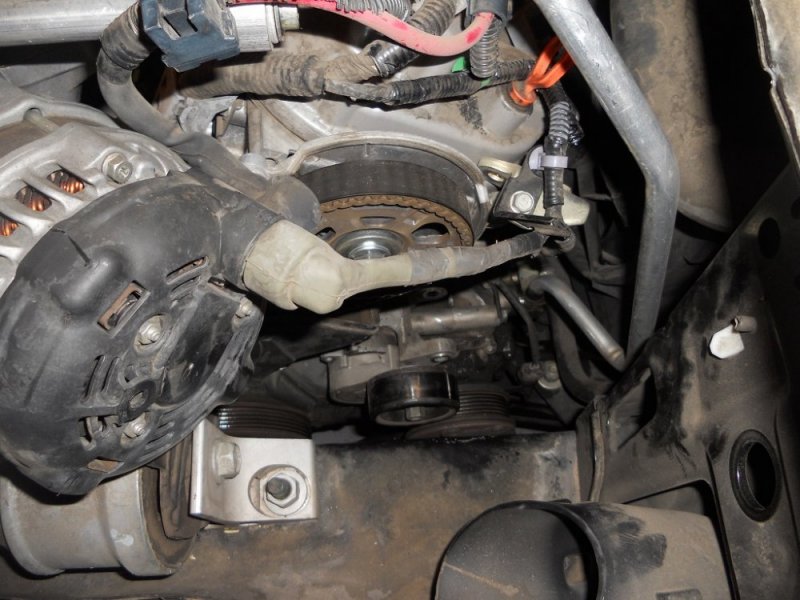
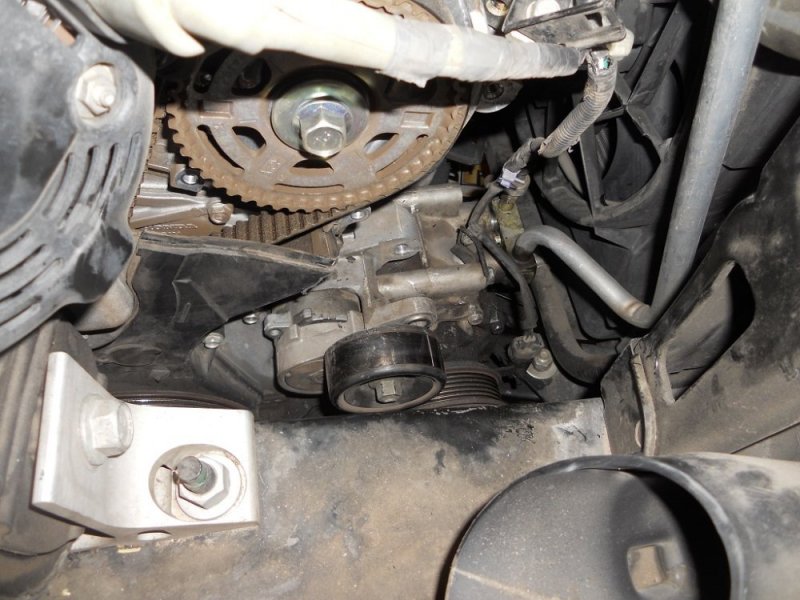
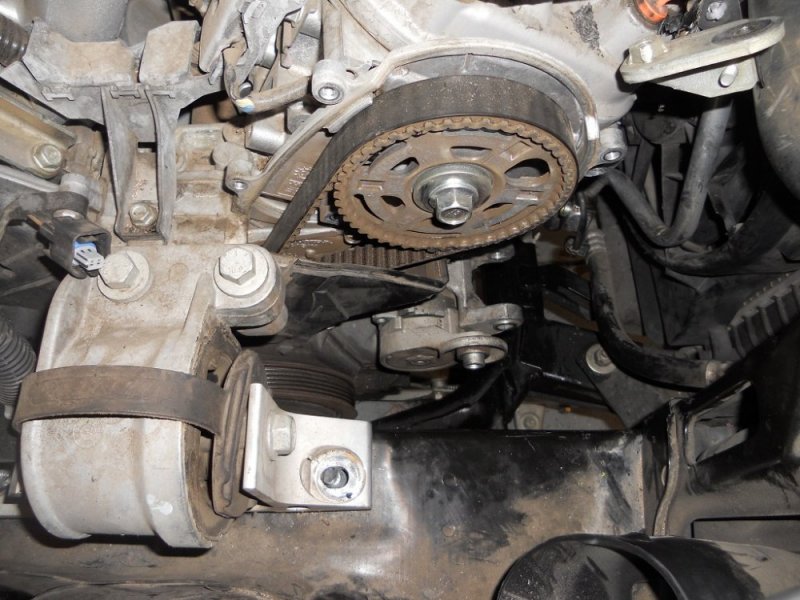
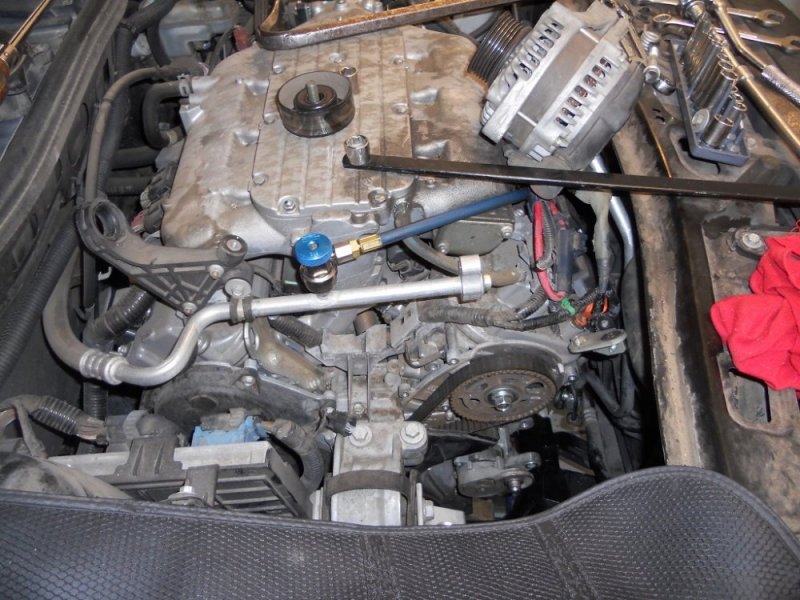
Seriously you need to make a video for a paragraph of text?!
Anyway got a 2007 Saturn Vue to replace the compressor on. Fighting it for a few years. First the AC Compressor Control Solenoid Valve failed in the "no cool at idle" position. You can get this part kit alone off fleabay or other places. You can change the valve by recovering the system, unbolting the compressor, and then the tilt of the compressor allows you to get to the valve located in the rear of the compressor from under the vehicle.
Couple years later the system lost it's charge with PAG oil all over the front of the compressor. A *cheep* recharge held another couple years.
Now it's time to rip the leaking compressor out. (The dryer is located behind the driver's side headlight. The headlight hooks the front bumper requiring some of the grille to be taken apart.) We removed the air cleaner box, timing belt cover, alternator, knocking the wire hold down on the rear of the alt off, then popping the two engine mount nuts off, top alternator bracket to valve cover, separating the AC line mid engine, removed tensioner pulley, and raising the engine some.
We used a section of scrap extension cord for a rope threaded through the compressor bolt holes to help pull the SOB out. The ports need to be rotated to the sky and clutch comes out first around the alt bracket. The AC hose needs to be moved out of the way taking 3 hands.
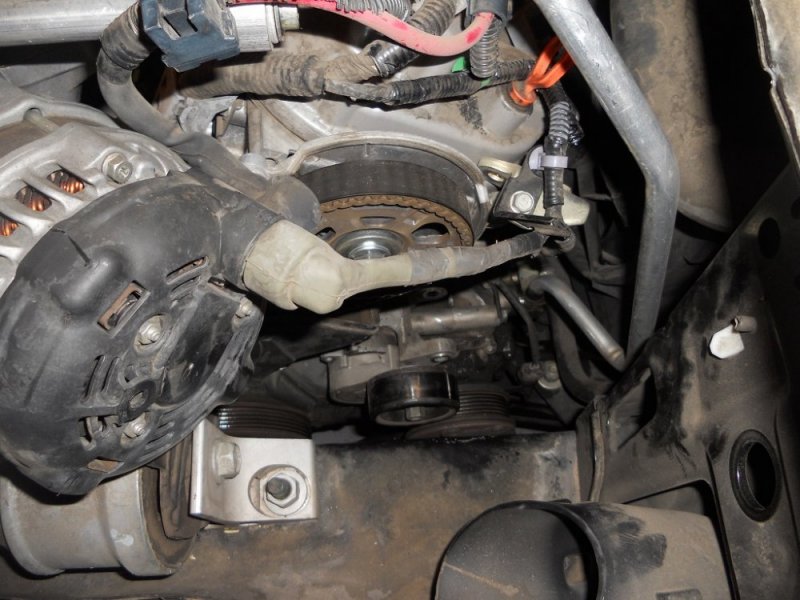
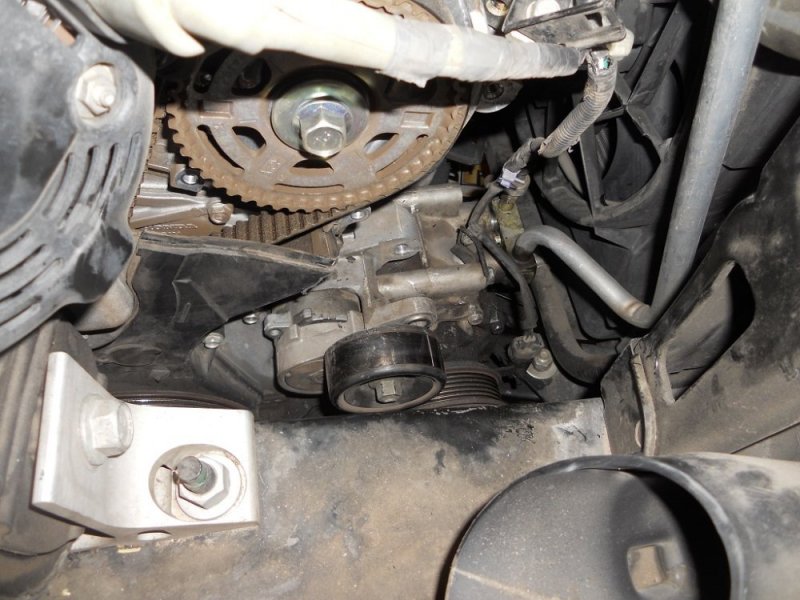
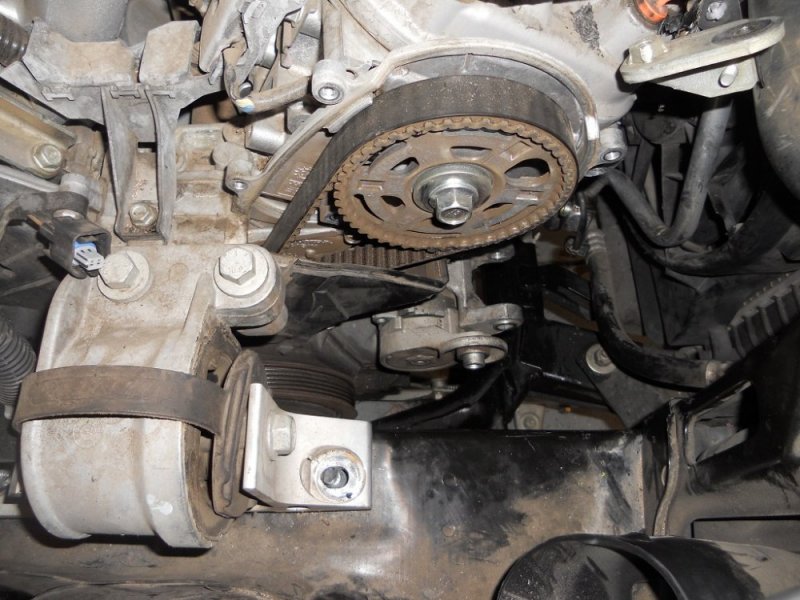
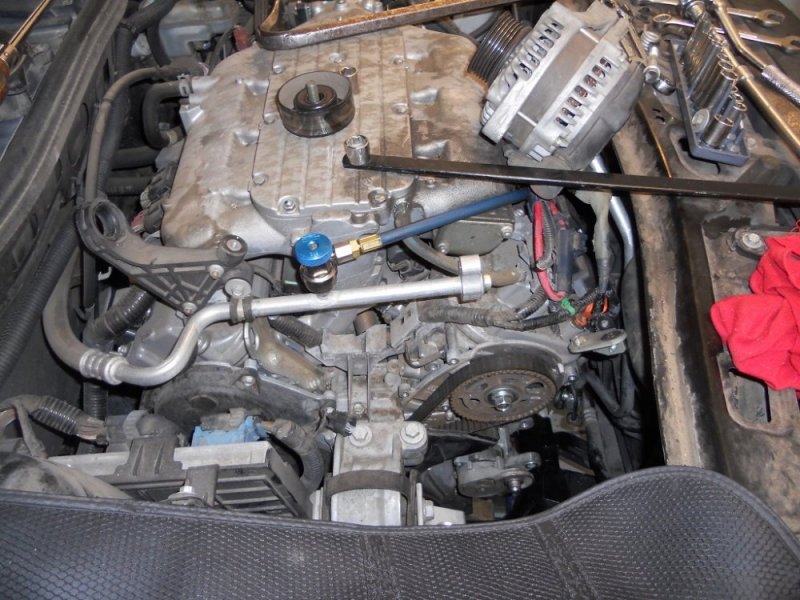