n8in8or
I never met a project I didn’t like
Right now I have a screen filter to keep junk out of the expensive Brassworks heater core in my 94 K3500. I did this because I got tired of the heater cores in my Tahoe getting plugged and needing to be replaced, so no way I was going to have that happen with this. Well the screen is doing a great job of keeping junk out, but unfortunately I’ve had to take it apart twice to clean it and I have less than 50 miles on the truck so far. I know you can buy bypass coolant filters you put in the heater hose to clean the whole system, but I don’t like the idea of any unfiltered coolant getting to the core. I have found a screw on coolant filter and a base it will go on so I’m good to go there, but I would like to monitor flow to the heater core when I do this for 2 reasons: 1. There wasn’t a flow rating for the filter, so I don’t know if it’s capable of flowing enough and 2. Since this isn’t a bypass filter and could potentially block all flow to the heater core, I want to have a flow meter in place so I can monitor the health of the filter. So with all that said, I need to know a good range to shoot for in a flow meter so I get good information. If it can flow 50gpm, a 5 gpm meter will be pretty useless and vice-versa. I’m just hoping someone can get me in the ballpark to start. I had initially considered just getting one of those visual flow indicators so I could see if it was still flowing, but I think it would be much more helpful to be able to grade the health of the filter rather than just say “yup, it’s still flowin’” or “dang, darn thing’s plugged up”….being able to monitor flow degradation will help me plan for replacement. I tried Googling for this info, but any answers I did find looked to be guesses. Thanks for any info!
Here’s my existing screen filter in the supply hose.
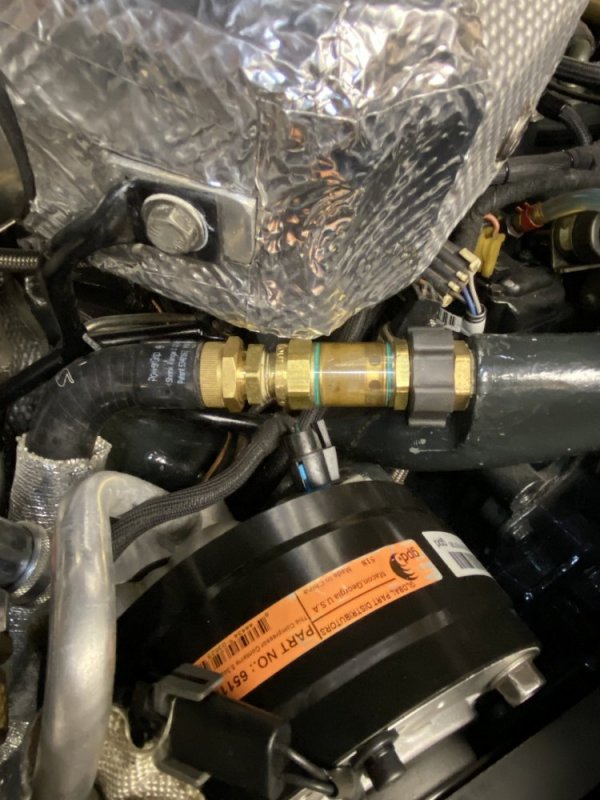
And here’s the filter and base I intend to install on the passenger fender. I also intend to have a bypass valve so if it does get blocked and it’s cold outside I can get heat in an emergency.
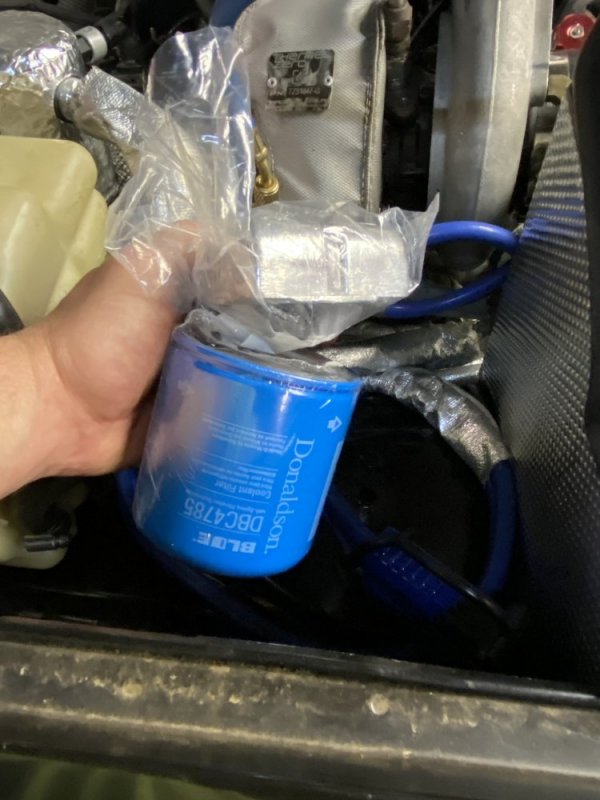
Here’s my existing screen filter in the supply hose.
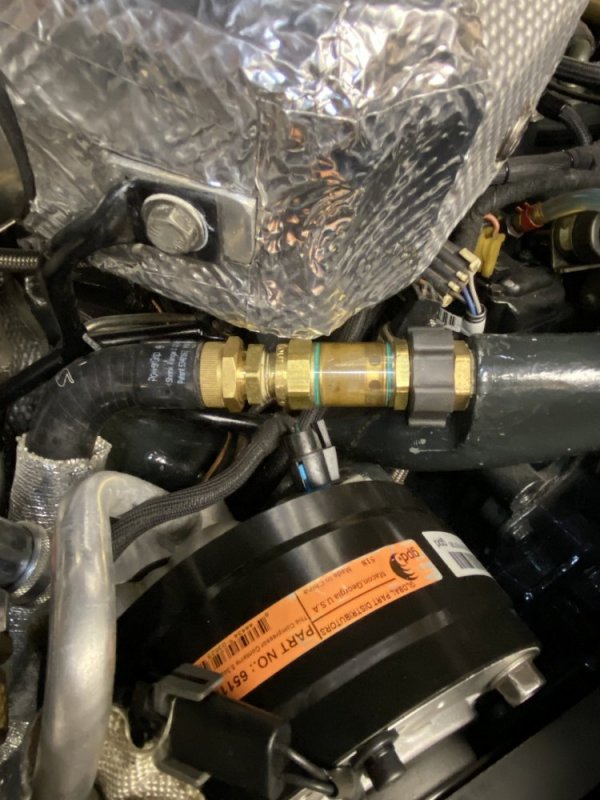
And here’s the filter and base I intend to install on the passenger fender. I also intend to have a bypass valve so if it does get blocked and it’s cold outside I can get heat in an emergency.
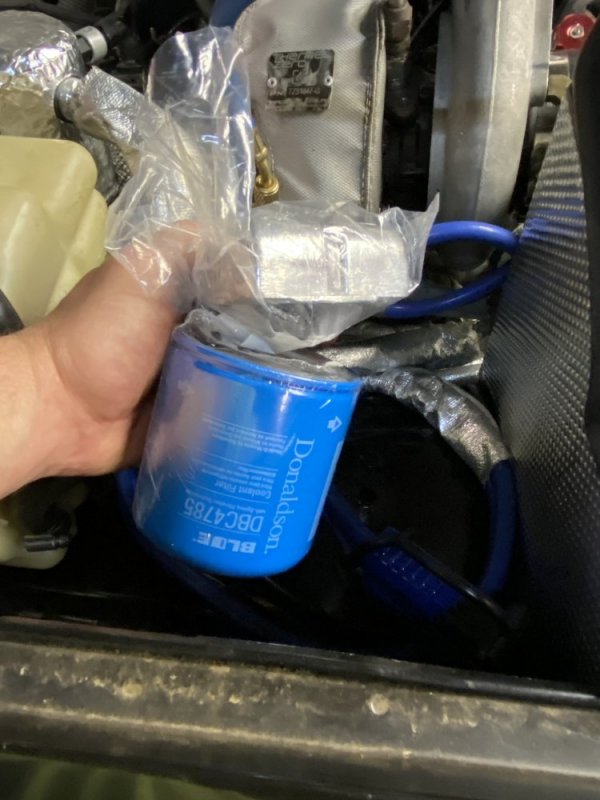