DieselAmateur
She ain't revved 'til the rods are thrown...
I was going to originally title this thread "Wet Hole Woes" but thought it a little too...well you get the picture. It is relevant though, here goes
So long story short I'm working on my multiyear K3500 1 ton Dump truck build. Sometime this spring a mud wasp had plugged up one of the holes in the front passenger cylinder head where the longest A/C compressor bolt goes through both mounting brackets and into the head. So I picked at the plugged hole with a piece of wire I had lying right there, sprayed a little WD40 into the hole to get the mud and dead insects inside to clump up, and pulled the majority of it out thinking I was done. Put a dab of antiseize on the threads, got it started by hand then put my little 12v ratchet to the bolt. A few turns, sounds like it's getting tight then POP! and it's loose. F@%!
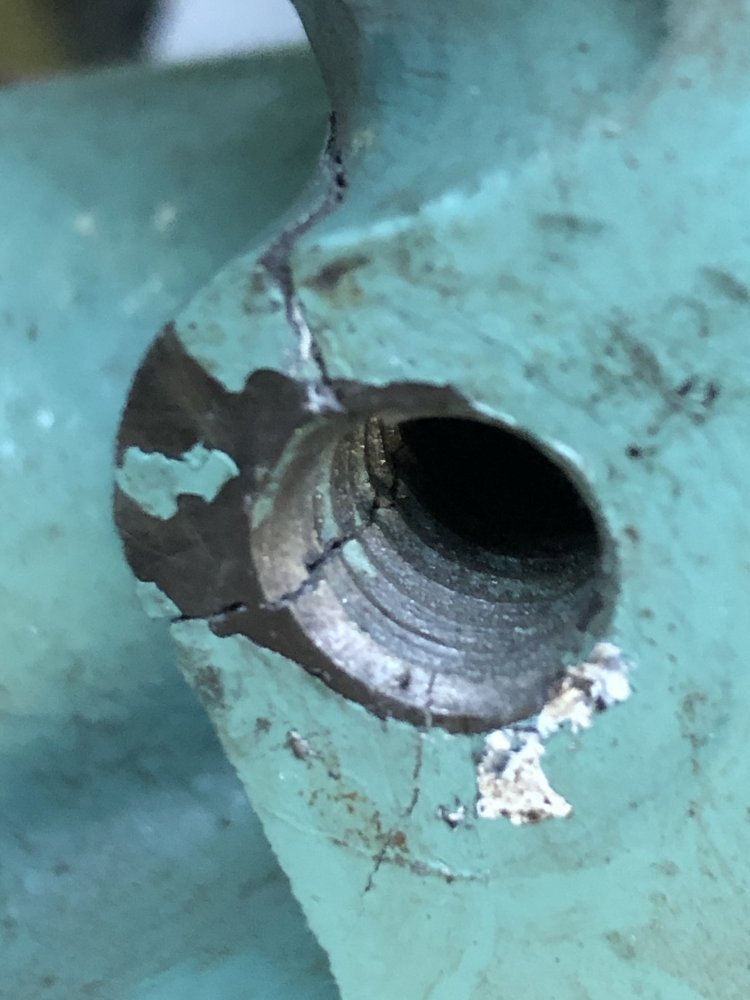
I've heard about wet holes causing cast iron to crack like this, but never encountered or experienced it myself until now. I had no idea the little bit of WD40 and antiseize would form a liquid that with 30ft lbs of torque from my puny cordless ratchet would crack a casting but this is just how my luck goes.
Both main cracks along the side do not meet. I tried to wiggle the piece out, not too hard but it seems pretty secure still. I can thread in the bolt and it has good bite. Here's a picture with a mirror showing both main cracks along the passenger side of the head moving towards the exhaust port
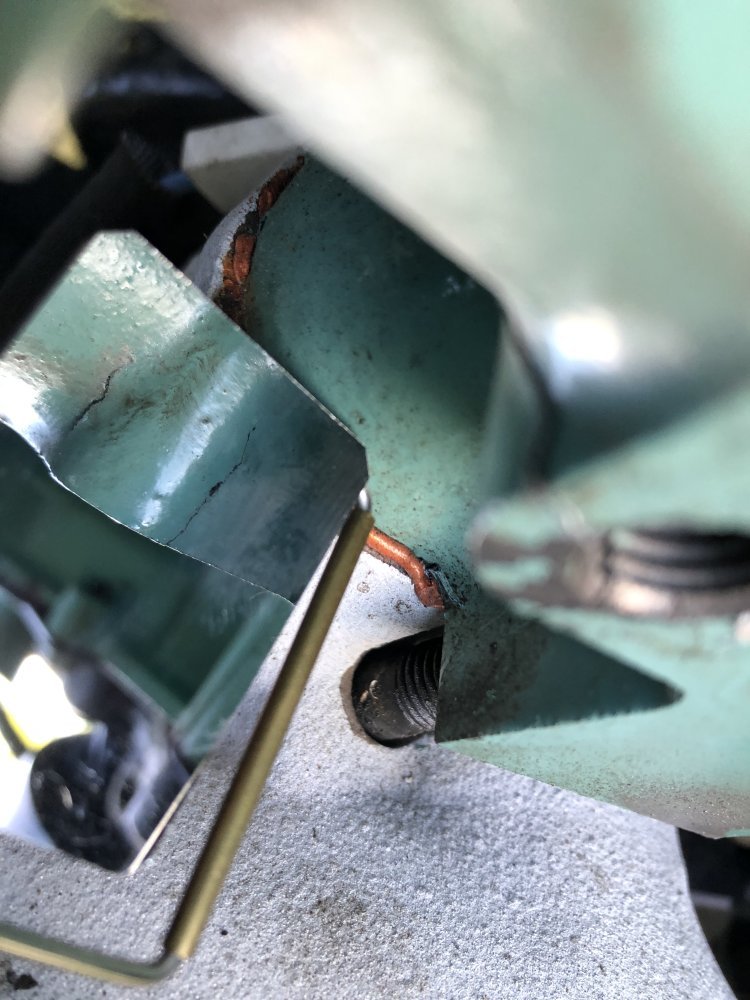
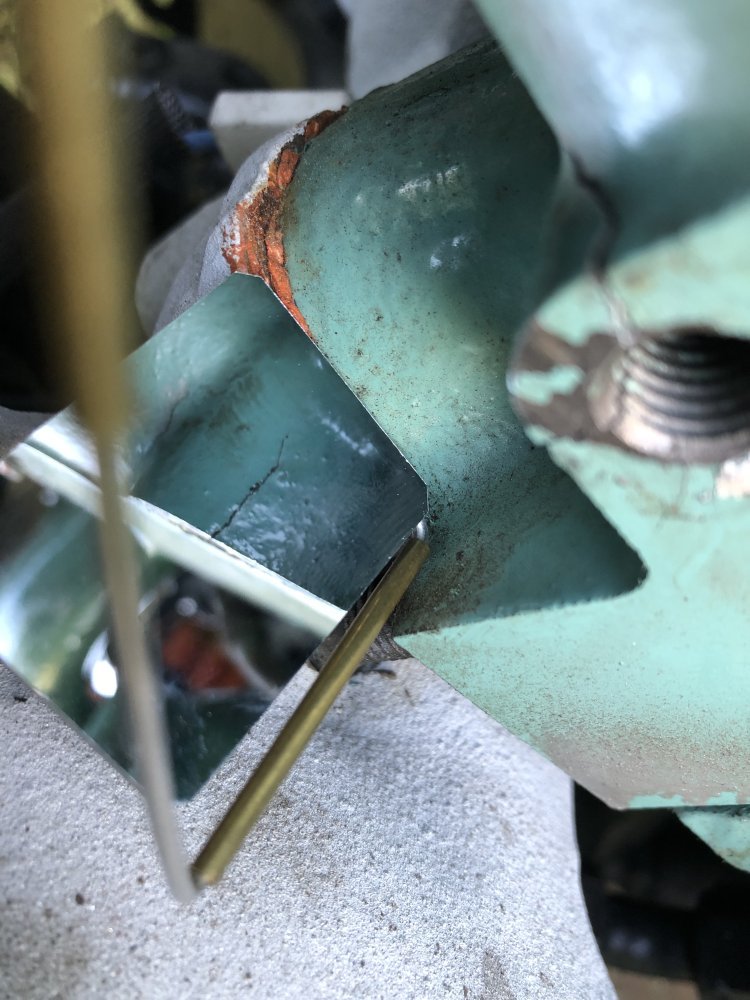
The lowermost crack doesn't appear to travel as far back as the upper one.
My main concern with the cracks, seeing as how they don't appear to travel all the way back to the end of the threads, is having them spread further and worst case scenario having the crack spread into a water jacket and causing big problems from there.
So before I cut into an old head to see what I'm dealing with behind these cracks (provided it's relatively similar geometry seeing as how this is a P400 head) does anyone know what lies behind/ between this threaded boss and the #2 exhaust port?
I am fairly certain that the only way to stop the cracks from spreading/ growing is to drill into the metal where the crack terminates. But I don't want to drill blind especially if there is a water jacket close by. Plus I'd have to remove the entire exhaust manifold and turbo and inner fender to get to the lower crack. Which I'm more than willing to do if it is the right course of action. But before I do the reverse parts cannon and start stripping the thing down, I'd love some advice from the experts as it's once again amateur hour here.
If given that I have good bite on the bolt still and there are several other bolts supporting the A/C compressor and bracket, what would the best course of action be to secure the bolt and prevent further cracking? Threadlocker? Make a brace that attaches to the bracket and is secured elsewhere on the engine and don't put a bolt in the threads at all?
I know lock n stitch makes inserts to repair situations like this, but they seem to be relocating and redoing their website as none of the links to their products work. An imitator named timesert makes a similar product but for $125 that sure is an expensive hole. Sorry I couldn't help myself
So long story short I'm working on my multiyear K3500 1 ton Dump truck build. Sometime this spring a mud wasp had plugged up one of the holes in the front passenger cylinder head where the longest A/C compressor bolt goes through both mounting brackets and into the head. So I picked at the plugged hole with a piece of wire I had lying right there, sprayed a little WD40 into the hole to get the mud and dead insects inside to clump up, and pulled the majority of it out thinking I was done. Put a dab of antiseize on the threads, got it started by hand then put my little 12v ratchet to the bolt. A few turns, sounds like it's getting tight then POP! and it's loose. F@%!
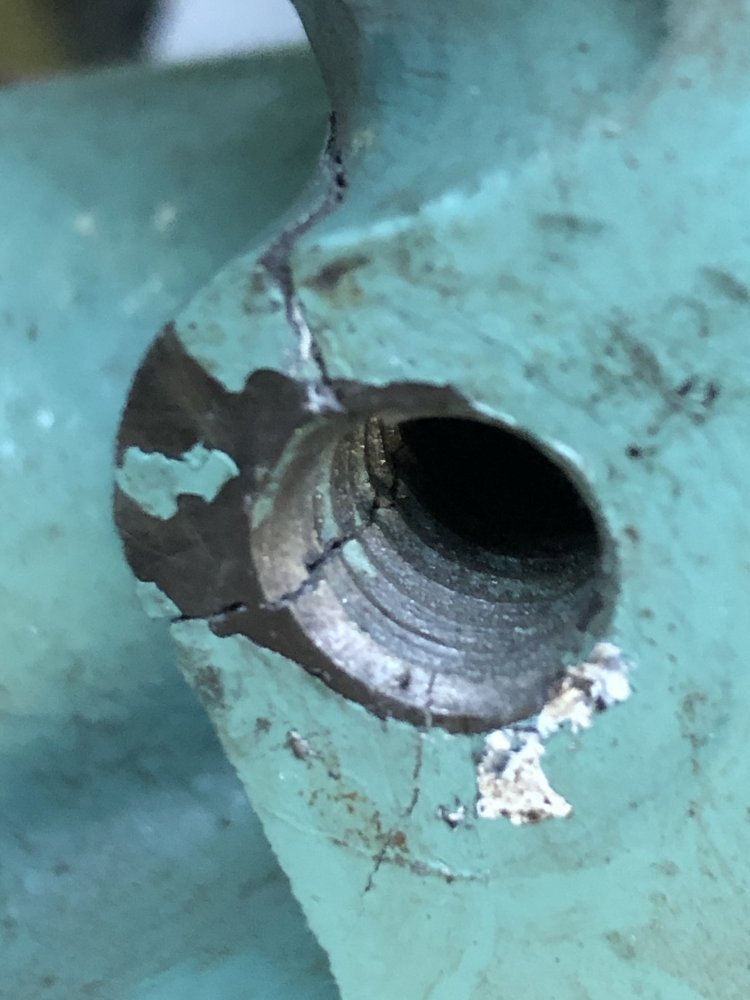
I've heard about wet holes causing cast iron to crack like this, but never encountered or experienced it myself until now. I had no idea the little bit of WD40 and antiseize would form a liquid that with 30ft lbs of torque from my puny cordless ratchet would crack a casting but this is just how my luck goes.
Both main cracks along the side do not meet. I tried to wiggle the piece out, not too hard but it seems pretty secure still. I can thread in the bolt and it has good bite. Here's a picture with a mirror showing both main cracks along the passenger side of the head moving towards the exhaust port
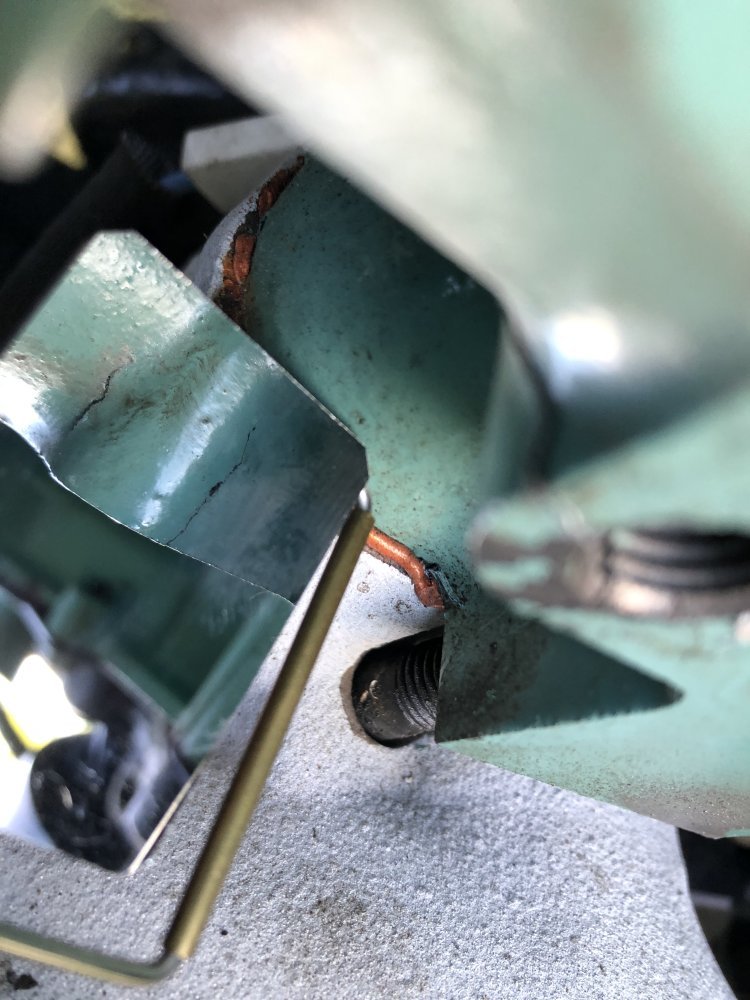
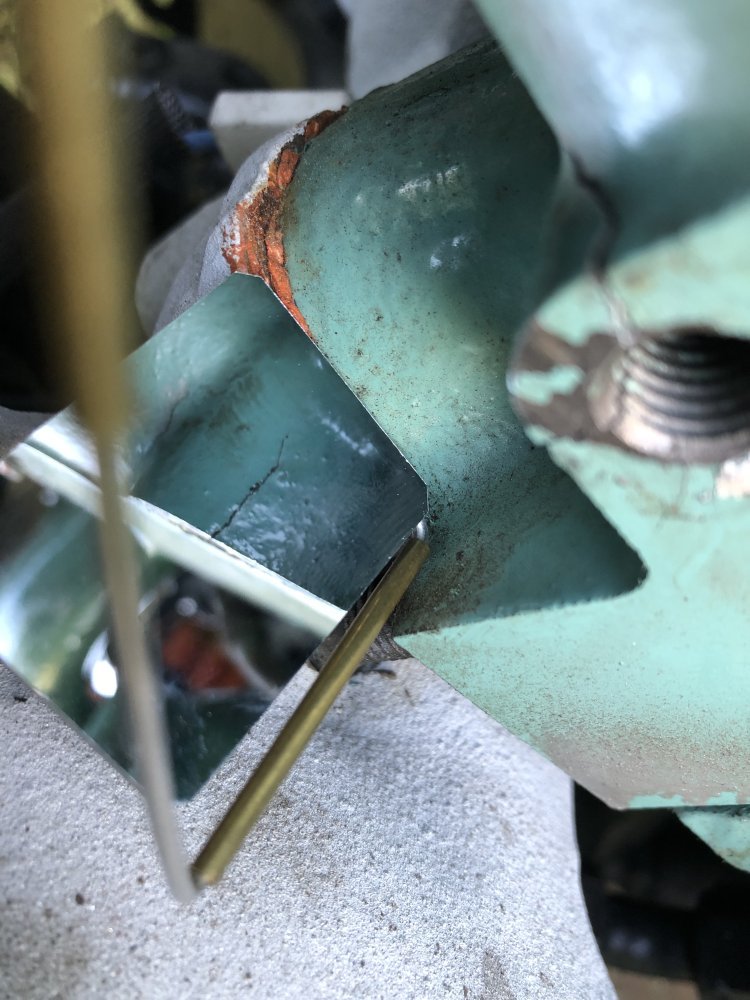
The lowermost crack doesn't appear to travel as far back as the upper one.
My main concern with the cracks, seeing as how they don't appear to travel all the way back to the end of the threads, is having them spread further and worst case scenario having the crack spread into a water jacket and causing big problems from there.
So before I cut into an old head to see what I'm dealing with behind these cracks (provided it's relatively similar geometry seeing as how this is a P400 head) does anyone know what lies behind/ between this threaded boss and the #2 exhaust port?
I am fairly certain that the only way to stop the cracks from spreading/ growing is to drill into the metal where the crack terminates. But I don't want to drill blind especially if there is a water jacket close by. Plus I'd have to remove the entire exhaust manifold and turbo and inner fender to get to the lower crack. Which I'm more than willing to do if it is the right course of action. But before I do the reverse parts cannon and start stripping the thing down, I'd love some advice from the experts as it's once again amateur hour here.
If given that I have good bite on the bolt still and there are several other bolts supporting the A/C compressor and bracket, what would the best course of action be to secure the bolt and prevent further cracking? Threadlocker? Make a brace that attaches to the bracket and is secured elsewhere on the engine and don't put a bolt in the threads at all?
I know lock n stitch makes inserts to repair situations like this, but they seem to be relocating and redoing their website as none of the links to their products work. An imitator named timesert makes a similar product but for $125 that sure is an expensive hole. Sorry I couldn't help myself
